I. Overview (Introduction)
In industrial drive equipment, the KEB COMBIVERT F5 series inverter is widely used in injection molding machines, elevators, and automation equipment. This series is renowned for its high stability and rich programmable functions. However, precisely due to its complexity, the prompt messages for different types of faults and the error evolution logic often confuse maintenance personnel during drive debugging and repair.
This article takes a real on – site fault as a clue, systematically sorting out the fault causes, parameter checks, and handling procedures from the initial E.OH (power module overheating) → subsequent recovery state E.nOH → E.H496 (extended error code) after replacing the motherboard. It also summarizes a standard troubleshooting logic to help you locate problems more efficiently.
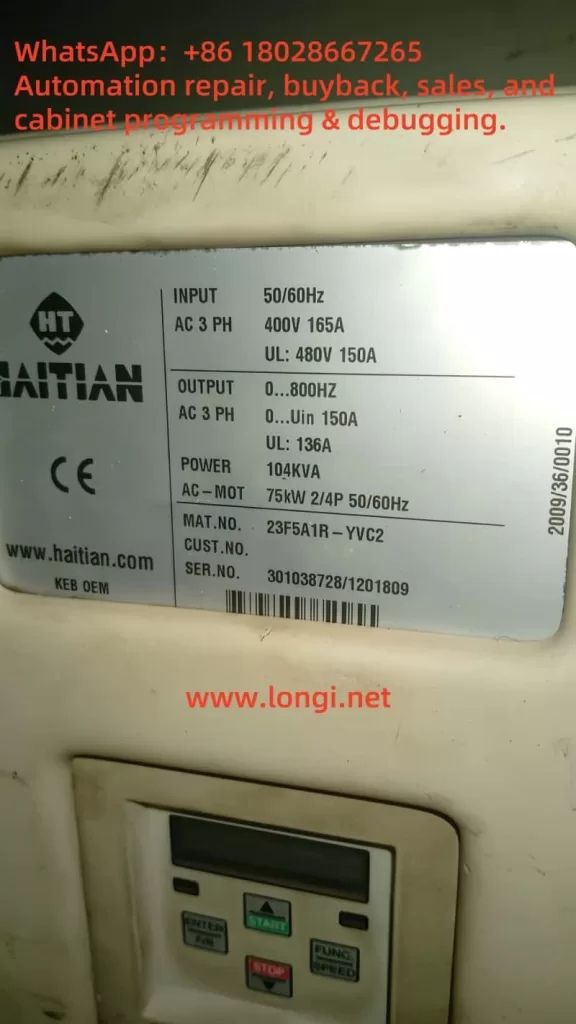
II. Drive Model and Hardware Background
- Model: KEB COMBIVERT F5 series (e.g., MAT.NO example: 23F5A1R – YVC2)
- Power rating: Approximately 75 kW, with an input of 400V AC three – phase, 165A; an output supporting a frequency range of 0 – 800 Hz, and a maximum current of about 150 A (UL 136A)
- Control board and power board combination: The drive unit is composed of an F5 – General or F5 – Basic control board in combination with a power module. The structured hardware connection is stable.
This system has undergone initial power – on, multiple fault resets, and motherboard replacement, eventually entering a complex error stage.
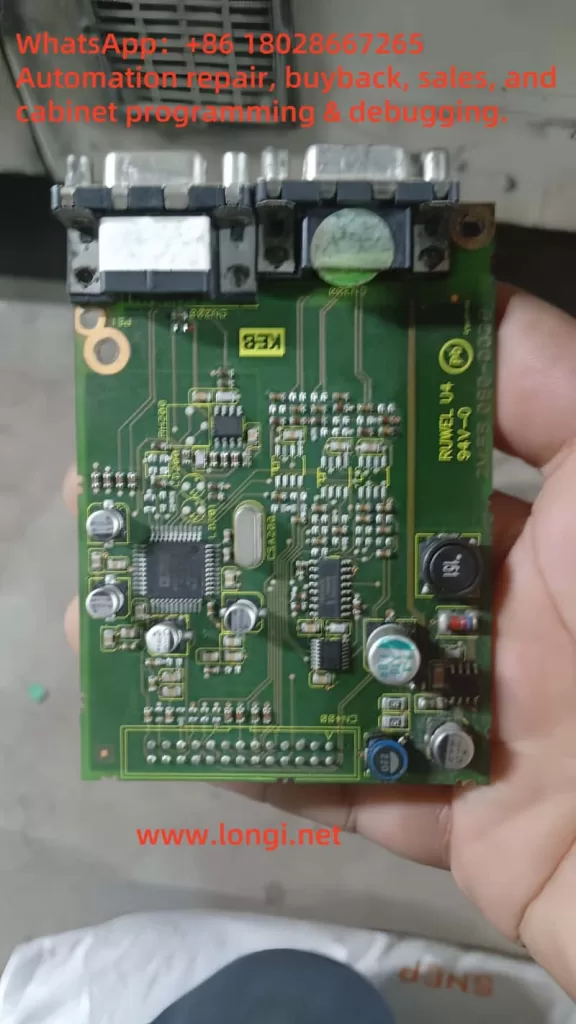
III. Stage 1: Initial Fault – E.OH (Power Module Overheating)
When the variable – frequency drive detects that the temperature of the power module (heat sink) is too high, it triggers the E.OH error, and at this time, the drive shuts off the output to protect the module. Such errors are often caused by:
- Blocked or failed cooling fans
- Severe dust accumulation on the heat sink
- Excessively high ambient temperature
According to the documentation (TRD Error codes / KEB F5 manual): - For E.OH, one must wait for the internal temperature to drop by at least 3 °C before entering the reset stage.
- The drive displaying E.nOH indicates that the overheating state has been lifted, and the power module has cooled to a safe level.
Maintenance operations include: - Powering off and waiting for cooling
- Cleaning the fans and heat sink
- Checking and improving the ambient ventilation
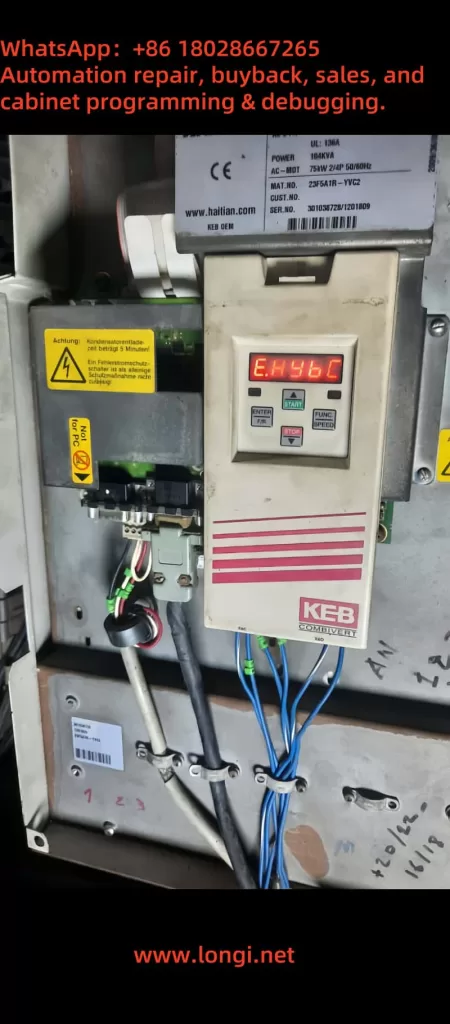
IV. Stage 2: From E.nOH to Replacing the Control Board
The E.nOH state confirms that the drive has returned to normal. Everything operates normally for a short period.
If the control motherboard is then replaced (e.g., replacing an old faulty board or upgrading the firmware), it may change the internal identification of the drive.
If the drive’s main control board and power board do not correctly match the firmware or power unit identification parameters at this time, new advanced errors may be triggered.
V. Stage 3: E.H496 – Advanced Extended Error Code After Replacing the Motherboard
1. What is E.H496?
E.H496 belongs to the advanced error code (extension error class), specifically indicating a communication or identification anomaly between the control board and the power unit.
In the KEB error manual, it is classified as “power unit changed” or “EEPROM configuration mismatch”. The error prompts may appear in forms such as E.PUCH, E.PUCH, etc., but some new firmware versions may display it as H496.
2. Cause Analysis
- The control board detects a change in the power unit identification number but the parameters are not synchronized.
- The power unit configuration saved in the EEPROM does not match.
- Inconsistent firmware versions lead to a failure in the parameter group SY.3 checksum.
- The physical connection between the control board and the power board is loose or the communication lines are loose.
VI. Standard Troubleshooting and Handling Procedures 🧭
Step 1: Check the Error History
- Set the parameter Ud.00 = 660 to enable the LF error log function.
- View the 0.LF.98 log to analyze the error generation time, type, and sequence.
Step 2: Verify the Connection between the Control Board and the Power Board
- Check whether the ribbon cables of the X interface are secure and free of oxidation.
- If there is dust or poor contact, clean and re – plug them.
Step 3: Confirm EEPROM and Firmware Matching
- Compare the firmware versions of the new and old motherboards with the power board version.
- If the drive prompts “power unit changed”, write the displayed power unit identification code into the parameter group SY.3 for confirmation.
- If the SY.3 parameter is written incorrectly, the system will load default values or lock the startup.
Step 4: Perform Synchronization and Initialization
- If there is an identification anomaly after replacing the control board, write the correct value of SY.3 according to the manual and only reload the power – related parameters.
- If it still fails, write other values to perform a complete parameter reload (load the KEB default set) and restart the drive.
- After completing the operations, it is recommended to restart the system (Power – on reset) to ensure synchronization between the drive board and the power module.
Step 5: Re – check Thermal Management and Hardware Status
- After cooling, power on again to ensure that the fans are working and the ambient temperature is reasonable.
- Avoid the recurrence of E.OH, which may affect subsequent diagnosis.
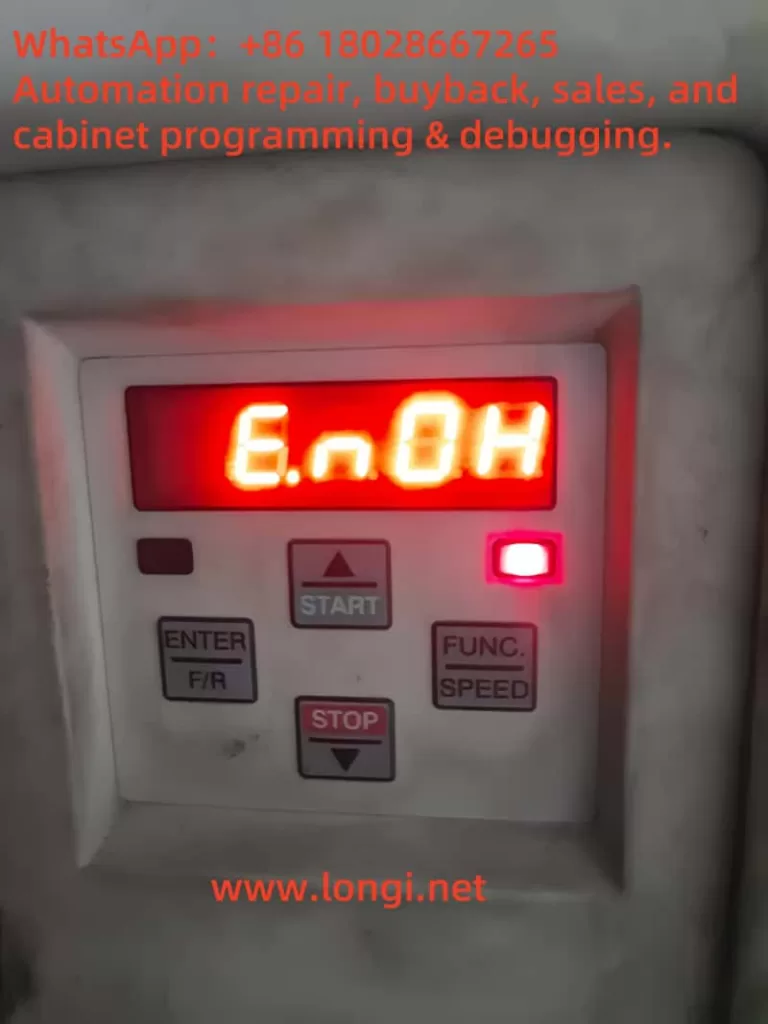
VII. Summary Table of Fault Evolution Logic
Stage | Display Code | Meaning | Possible Causes | Main Handling Measures |
---|---|---|---|---|
Initial | E.OH → E.nOH | First overheating of the power module and return after cooling | Poor heat dissipation, high ambient temperature | Clean the fans and heat sink, improve ventilation |
Intermediate | E.nOH state returns to normal | No new errors in the module | Temporary parameter recovery process | No additional operations required |
After replacing the motherboard | E.H496 or E.PUCH | Advanced error: Power unit identification anomaly | Control board/firmware mismatch, identification code change, communication error | Rewrite SY.3, check communication, re – initialize parameters |
VIII. Recommended Further Operation Plans and Prevention Points
- Record the LF error log
Save the LF.98 content completely before and after state switching to facilitate tracing the root cause of errors. - Synchronize parameter groups after replacing the motherboard
Especially for SY.3 and related LF/enc parameters, confirm that the motherboard and power module are properly matched. - Fan and ventilation maintenance
Regularly maintain the cooling system to avoid long – term dust accumulation and overheating faults. - Perform encoder reset and learning (if applicable)
If there has been a recent replacement of the encoder card or a change in the feedback interface, check parameters such as LF.26 and LF.27 and re – execute the automatic learning process (refer to the previous handling of E.HYBc – type errors). - Collaborate with KEB technical support if necessary
If the firmware version is unclear or the error code is ambiguous, provide information such as SY.3 / LF.98 to KEB support engineers for targeted guidance.
IX. Conclusion
The process from E.OH (power module overheating) → recovery to E.nOH → entering the E.H496 advanced error after replacing the motherboard actually reflects the strong mechanism of KEB drives for hardware identification and power unit consistency verification. Reasonable understanding and operation according to the standard procedures can minimize the fault recovery time and improve equipment stability.