The ParticleTrack G400 from Mettler‑Toledo is an advanced in situ particle analysis system based on Focused Beam Reflectance Measurement (FBRM®) technology. It enables real-time, direct measurements of particle size and count in full-concentration processes without the need for sampling or dilution. This comprehensive guide explains the working principle, installation, configuration, calibration, operation, maintenance, troubleshooting, and advanced integration options of the ParticleTrack G400 system. It is designed to support users from first-time setup to expert-level deployment in laboratory or process environments.
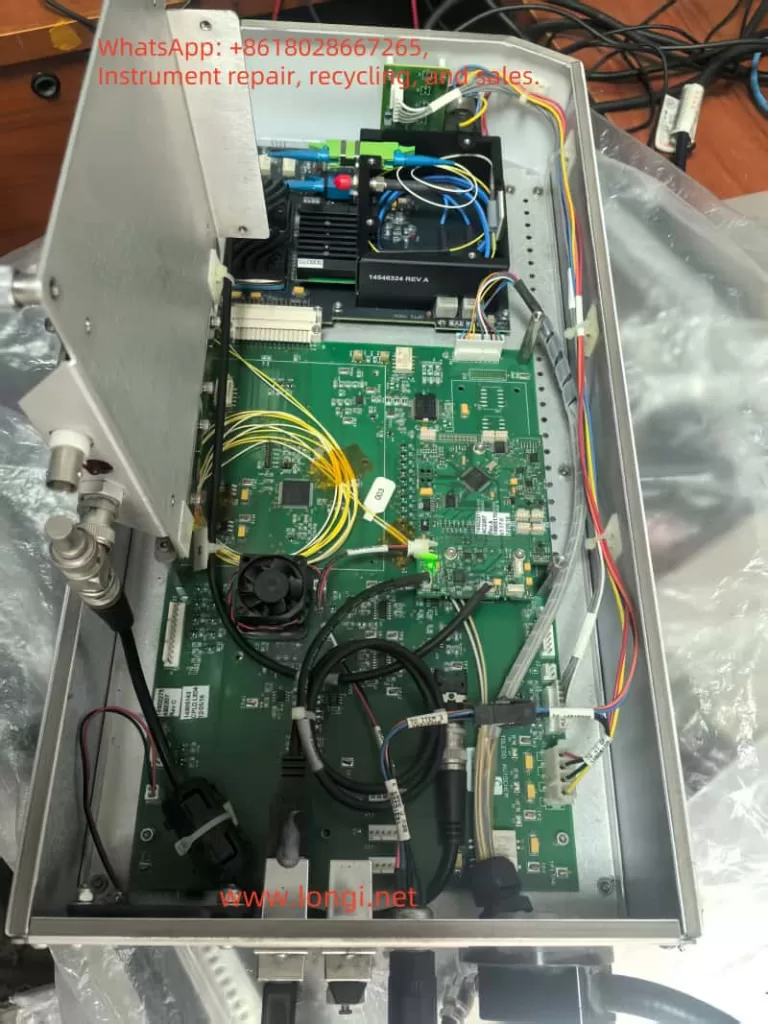
1. Working Principle and Key Advantages
The ParticleTrack G400 uses a rotating 780 nm laser beam focused just beyond the sapphire window of the probe. When the beam intersects a particle or droplet, it reflects back to the detector. The duration of this reflection is converted into a “chord length”, allowing the system to calculate particle size distributions in real time.
Key advantages include:
- True in-situ analysis without the need for sample extraction or dilution.
- Wide dynamic range measuring particles from 0.5 µm to 2 000 µm.
- Real-time monitoring, with updates as frequently as every second.
- Modular probe design, including interchangeable tips for different reactor volumes.
- Process-resilient construction, handling temperatures from –80 °C to +90 °C and pressures up to 100 bar.
2. System Components and Safety Considerations
Component | Description | Key Specifications |
---|---|---|
Base Unit | Houses laser, motor, signal processing hardware | 100–240 VAC, USB, 3.25 kg |
FBRM Probe | Sensor head for immersion in process stream | Available in 14 mm / 19 mm diameters |
Software (iC FBRM) | Interface for configuration, data capture, analytics | Windows-based, OPC UA/DCS compatible |
Safety Notes:
- The system is classified as a Class 1 laser product and is safe under normal operating conditions.
- Only trained personnel should handle system components.
- The internal laser module and electronics are not user-serviceable.
- Always ensure the system is properly grounded and installed indoors.
3. Installation and Probe Positioning
Installation steps:
- Hardware setup:
- Connect the AC power supply and USB cable to the computer.
- Confirm the “Power” and “HW-Status” LEDs are illuminated steadily.
- Process positioning:
- Install the probe in a location where flow is continuous and representative.
- The sapphire window should face the flow direction at a 30°–60° angle, ideally 45°, to maximize measurement accuracy and reduce buildup.
- Optional air purge:
- In cold or humid environments, connect clean, dry instrument air at 1 barg during start-up, then reduce to 0.15 SLPM to avoid condensation.
4. Software Operation (iC FBRM 4.4)
4.1 Experiment Setup
- Open iC FBRM.
- Select New Experiment.
- Enter a name, define the data storage path, set the total run duration, and choose a measurement interval (e.g., 1s, 5s, 30s).
4.2 Real-Time Monitoring
- Color-coded status indicator:
- Green: Running
- Yellow: Paused
- Red: Error
- Blue: Stopped
- You can annotate events (e.g., reagent addition) directly onto live trends.
4.3 Data Review & Reporting
- Use Trend Viewer to monitor D50, counts/sec, and chord counts over time.
- Distribution Viewer displays real-time and historical chord length distributions.
- Statistics Viewer shows mean, mode, and percentile summaries.
- Export data to Word, Excel, PDF, or CSV for documentation or analysis.
5. Calibration and Validation
Task | Frequency | Purpose |
---|---|---|
Calibration Validation | Every 3–6 months or after a fall | Verifies scan geometry and optical alignment |
Chord Selection Model | Before each new experiment | Optimize detection for fine/coarse particles |
Validation procedure:
- Use the Calibration Validation Wizard in iC FBRM.
- Mount a standard PVC reference sample in a fixed beaker stand.
- Run validation and compare results to reference data.
- Acceptable deviation: less than 5%; if more than 10%, clean or inspect optics.
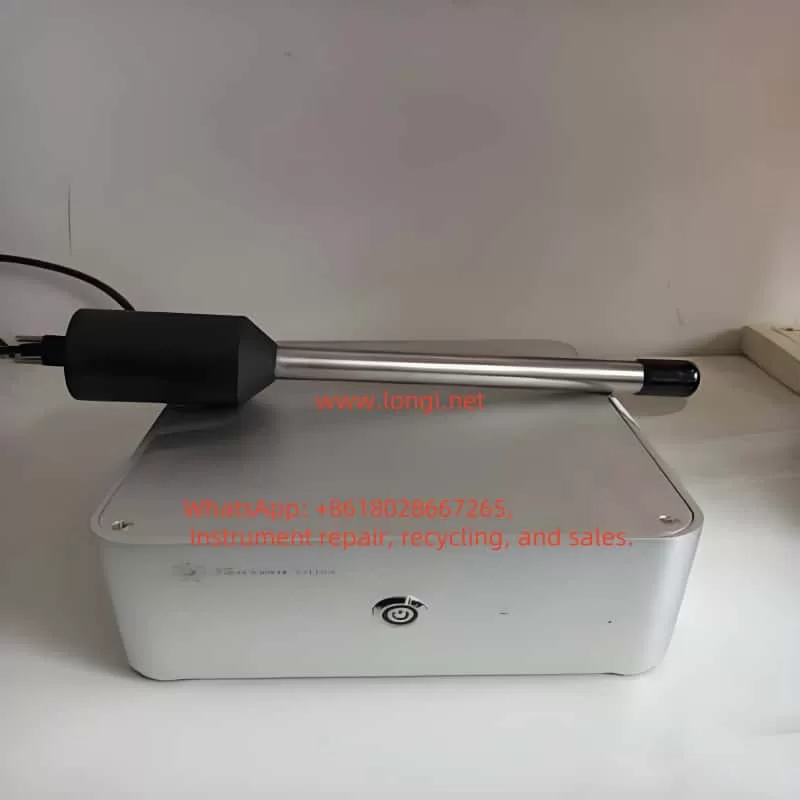
6. Maintenance and Cleaning
Routine practices:
- Window cleaning:
- Wipe using Kimwipes moistened with distilled water, ethanol, or acetone.
- For stubborn residue, use a fine (0.3 µm) alumina polishing compound.
- Air purge maintenance:
- Maintain steady 0.15 SLPM during operation.
- Shut off only after cool-down to prevent condensation.
- Preventive Maintenance (PM):
- Replace probe tip or rotary bearings every 1–2 years depending on use.
- Keep software updated to enable PM alerts and tracking.
- Storage:
- After use, store the probe upright and dry in a protective case.
7. Troubleshooting
Issue | Possible Cause | Action |
---|---|---|
Scan Speed Too Low | Worn bearings or incorrect configuration | Replace bearings; verify probe type in software |
No Counts | Window fouled or probe not immersed | Clean window; check immersion depth |
Signal Intensity Too High | Reflective particles causing saturation | Switch to Macro CSM or dilute sample |
Data Acquisition Error | USB or PC performance issue | Reconnect cable; adjust interval or upgrade PC |
Tach Pulse Missing | Faulty motor or encoder | Contact technical support |
Note: The internal electronics are not user-repairable. For serious hardware faults, contact Mettler-Toledo for Return Material Authorization (RMA).
8. Extended Capabilities
- Dual System Operation:
- You may connect two G400 units to a single computer for simultaneous monitoring.
- Configure each instrument separately in the software.
- OPC UA / Modbus Integration:
- Allows real-time data output to SCADA or DCS systems.
- Enables feedback control loops for crystallization and particle formation processes.
- Data Archiving:
- Integrate with iC Data Center for secure storage of all measurement records in GMP-compliant formats.
9. Best Practices
- Pre-warm the probe 30 minutes before use.
- Choose appropriate measurement intervals:
- 1–5 s during fast transitions (e.g., seeding),
- 30–60 s during stable phases to reduce file size.
- Avoid installing probes parallel to vessel walls or facing baffles.
- Always validate the system before starting critical experiments.
- Participate in Mettler-Toledo AutoChem training webinars for advanced topics.
10. Conclusion
The ParticleTrack G400 is a powerful and precise tool for monitoring particle dynamics in real time, directly within your process. By following the installation, calibration, and maintenance recommendations provided in this guide, users can achieve high-quality, reproducible measurements that enhance process understanding, control, and optimization. Whether you’re conducting crystallization research, scaling up emulsions, or controlling flocculation, the G400 provides data you can trust.