1. Introduction
In industrial emission monitoring, combustion control, and process analysis, gas analyzers play a critical role in ensuring safety, efficiency, and compliance with environmental standards. The ABB EL3020 is a widely used multi-component gas analyzer based on infrared optical measurement principles. It is designed to continuously monitor gases such as CO, CO₂, NO, and SO₂ in various industrial applications.
However, during long-term operation, users may sometimes encounter abnormal readings, the most common of which is negative CO concentration values. Such readings do not imply the physical existence of “negative carbon monoxide,” but instead reflect calibration drift, background interference, or hardware-related issues.
This article provides a detailed explanation of the EL3020’s measurement principle, analyzes the possible causes of negative CO readings, and presents practical zero calibration and span calibration procedures. The aim is to help engineers and operators quickly identify the root cause, restore measurement accuracy, and ensure stable operation of the analyzer.
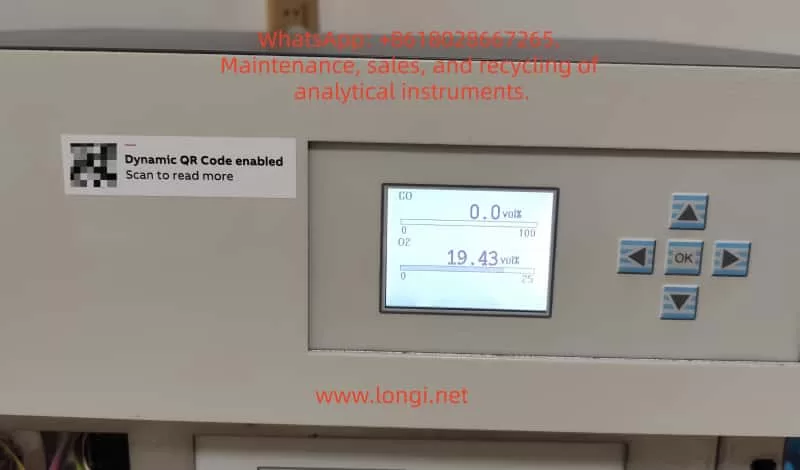
2. Operating Principle of ABB EL3020
2.1 Infrared Absorption Principle
The EL3020 operates on the principle of non-dispersive infrared absorption (NDIR).
- Each gas molecule has a unique absorption band in the infrared spectrum.
- When an infrared beam passes through a sample gas containing CO, the CO molecules absorb energy at specific wavelengths.
- The detector measures the reduction in light intensity, which is directly proportional to the gas concentration.
- By comparing the reference and measurement channels, the analyzer calculates the gas concentration.
2.2 Zero and Span Definitions
- Zero Point: The output signal when no target gas is present (pure zero gas condition). Ideally, the instrument should display 0 ppm.
- Span Point: The output when a known concentration of calibration gas is introduced. Span calibration adjusts the slope factor to ensure linear accuracy.
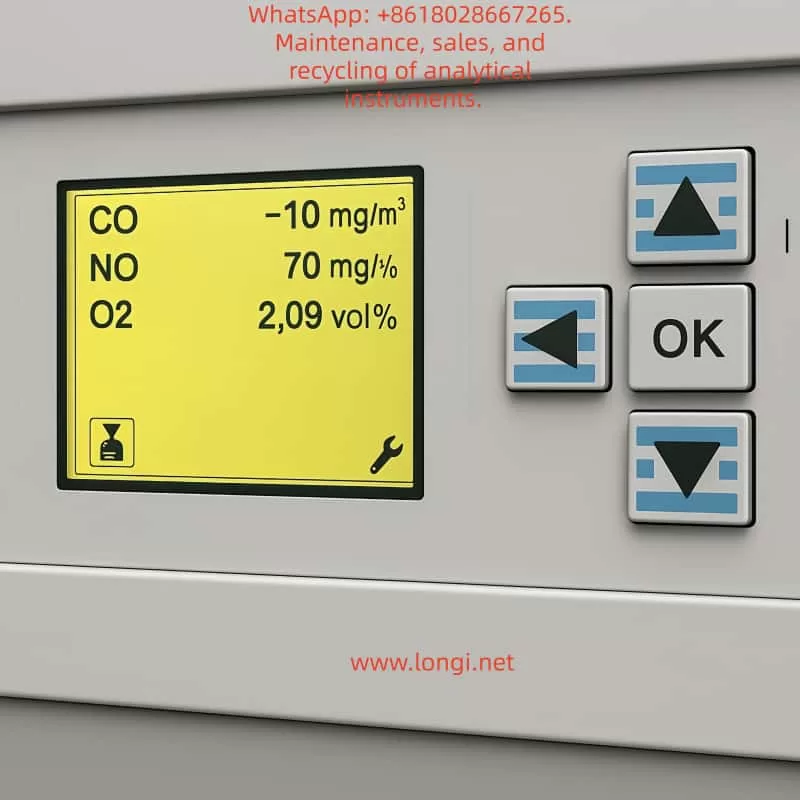
3. Causes of Negative CO Readings
3.1 Zero Drift
Over time, detector electronics and optical components may drift due to temperature variations and aging. If the zero point is not recalibrated, the baseline may shift below zero, producing negative values.
3.2 Background Interference
If the sampled gas contains almost no CO while the instrument’s baseline is incorrectly set too high, the computed result may fall below zero. Excess oxygen, water vapor, or other gases can also disturb the optical path.
3.3 Optical Contamination or Aging
Dust, condensation, or weakened infrared sources reduce the signal strength at the detector, leading to baseline shifts.
3.4 Hardware or Circuit Faults
Faults in the analog acquisition board, A/D converters, or signal amplifiers can also cause abnormal negative readings. If only the CO channel is affected while NO and O₂ are stable, the issue likely lies in the CO detection unit.
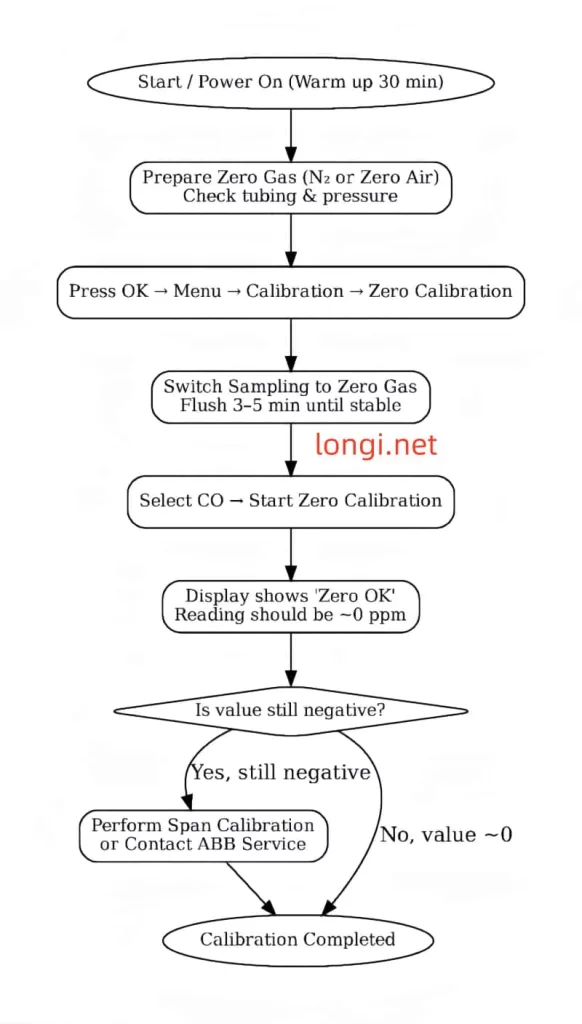
4. Zero Calibration Procedure
Zero calibration eliminates baseline drift and resets the analyzer output to zero under clean gas conditions.
4.1 Preparation
- Use high-purity nitrogen (99.999%) or certified zero air as the zero gas.
- Verify gas purity and set regulator output pressure to ~2 bar.
- Check sample lines for leakage or condensation.
- Power on the analyzer for at least 30 minutes to stabilize.
4.2 Step-by-Step Process
- On the panel, navigate: OK → Menu → Calibration → Zero Calibration.
- Select the CO channel.
- Switch the sample inlet to zero gas and flush for 3–5 minutes until stable.
- Execute Start Zero Calibration.
- After completion, the CO value should display close to 0 ppm (±2 ppm acceptable).
4.3 Evaluation
- If “Zero OK” appears and the reading stabilizes, calibration is successful.
- If negative values persist, further action such as span calibration or hardware inspection may be required.
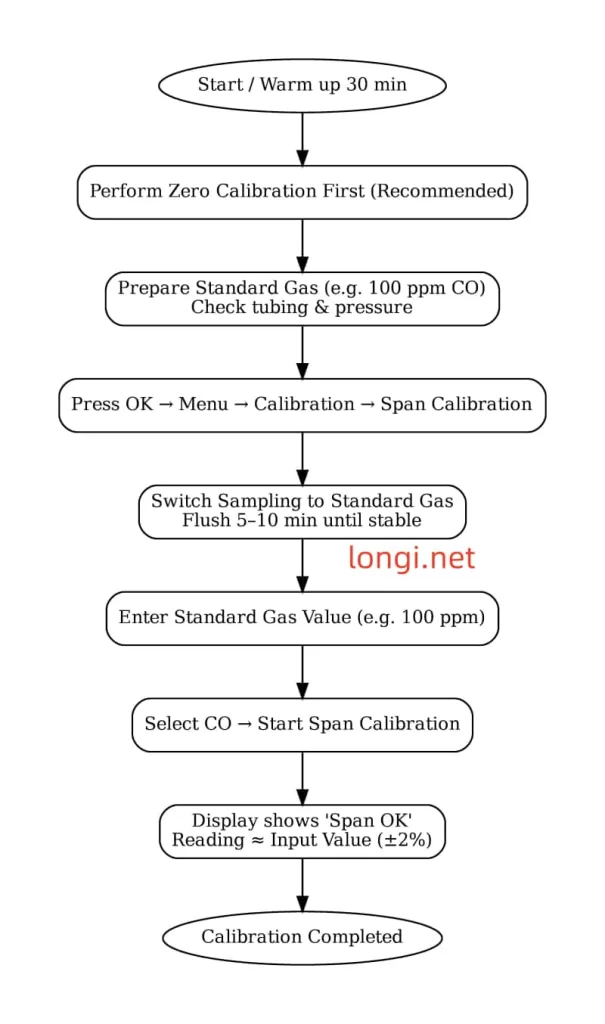
5. Span Calibration Procedure
Span calibration corrects the proportionality factor (slope) to align measured values with certified standard gas concentrations.
5.1 Preparation
- Use certified CO span gas, preferably at 60–90% of the measurement range (e.g., 100 ppm CO in N₂).
- Check cylinder, pressure regulator, and tubing for leaks.
- Perform zero calibration before span calibration for best results.
5.2 Step-by-Step Process
- On the panel, navigate: OK → Menu → Calibration → Span Calibration.
- Select the CO channel.
- Switch the sample inlet to the standard gas and flush for 5–10 minutes until stable.
- Enter the certified gas concentration (e.g., 100 ppm).
- Execute Start Span Calibration.
- The analyzer adjusts the slope factor and confirms with Span OK.
5.3 Evaluation
- If the analyzer output matches the certified value (within ±2%), span calibration is successful.
- Large deviations indicate optical degradation or electronic faults that may require service intervention.
6. Maintenance and Troubleshooting Recommendations
- Regular Calibration
- Perform zero calibration monthly and span calibration every 1–3 months.
- Optical Cleaning
- Inspect and clean optical windows and gas cells regularly. Prevent dust and moisture accumulation.
- Sample Line Maintenance
- Avoid condensation and leaks in tubing. Use filters and dryers where necessary.
- Validation with Reference Gas
- Periodically validate with independent standard gas to ensure accuracy.
- Hardware Inspection
- If calibration fails, check the infrared source, detectors, and analog boards. Replace if necessary.
7. Case Study: Negative CO Reading Restored by Calibration
In a steel plant, operators observed the EL3020 CO channel consistently showing -5 ppm.
- Zero calibration with nitrogen reduced the offset, but the value remained at -3 ppm.
- A span calibration using 100 ppm CO gas showed the analyzer reading 95 ppm.
- After span adjustment, the zero point stabilized near 0 ppm and span response matched 100 ppm.
The issue was traced to slope drift in the CO channel, which was successfully corrected through calibration without requiring hardware replacement.
8. Conclusion
The ABB EL3020 is a reliable and accurate gas analyzer for continuous industrial monitoring. Negative CO readings are typically not measurement of “negative concentration” but symptoms of baseline drift or span factor deviation. Proper and regular zero calibration and span calibration are essential to maintain measurement accuracy.
For persistent negative values that cannot be corrected through calibration, optical contamination, component aging, or hardware malfunction should be considered. Timely maintenance and service support are key to ensuring the long-term stability of the analyzer.
By following standardized calibration procedures and maintenance practices, operators can keep the EL3020 functioning accurately and extend its service life in demanding industrial environments.