The ATV71 inverter displays a message at the top of the screen stating “Last fault occurred Brake control,” with status words listed below (ETA state word 0037 Hex, ETI state word 8812 Hex, Cmd word 000F Hex). This indicates that the last fault was related to brake control. Based on the documentation, we determine that this corresponds to fault codes “brF” or “bLF,” which are typical indicators of feedback anomalies or release failures detected by the brake controller.

I. Fault Meaning and English Title
In the manufacturer’s documentation, such faults are referred to as “Brake feedback fault” or “Brake control fault.” The Chinese translations are often “Mechanical brake feedback fault” or “Brake control fault.”
- sl1: When the brake feedback contact signal does not match the internal logic of the inverter, a brF error is immediately triggered.
- sl2: When incorrect parameter settings or improper brake current and logic control prevent the brake from releasing correctly, this fault is also indicated.
II. Main Causes of the Fault
1. Abnormal Brake Feedback Contact Status
The internal logic expects the electromagnetic brake to be in a certain state (open or closed), but the actual feedback does not match, leading to the assumption that the brake has not been released or closed, thus triggering the fault.
2. Insufficient Brake Release Current / Improper Parameter Settings
Parameters Ibr (forward) and Ird (reverse) represent the brake release current thresholds. If these are set too low, they may not provide enough energy to the brake (controlled via GPIO), preventing it from releasing.
3. Unreasonable Brake Release Time Settings
Parameters bEn (brake closing frequency/logic control related) and bEt (brake release time), if not set or set unreasonably, can cause the inverter to mistakenly believe that the brake has failed to release and trigger a fault.
4. Brake Mechanical or Feedback Unit Fault
Brake bushing wear, spring fatigue, coil disconnection, feedback switch disconnection, or loose wiring can all cause inconsistencies between the mechanical state and the logic.
5. Brake Unit Electrical Short Circuit (bUF Error)
Although not identical to brF, a short circuit in the brake unit can also trigger a logic-based brake failure.
III. Manufacturer’s Official Setting Recommendations
- Enable Brake Logic Parameters in Expert Mode
- Parameter brH b2: If set to “1,” feedback contact confirmation is included in the brake release logic; if set to “0,” only the preset time is relied upon.
- Parameter bEt (Brake Engage/Release Time): Set to a value not less than the actual inertial closing time required by the brake. For example, if the actual time is approximately 1s, set it to at least 1s or more. Otherwise, a fault will be认定 (determined) if the feedback does not close within the time limit.
- Calibrate Brake Release Current Parameters
- Adjust Ibr and Ird to ensure they provide sufficient current to fully release the brake.
- Check Feedback Logic
- Verify that the feedback contacts are correctly connected to the digital inputs, the control logic is properly assigned, and the wiring is correct.
IV. Comprehensive Fault Troubleshooting Process
Based on the above information, the following systematic process is summarized:
✅ Step 1: Reset and Confirm Fault Recurrence
- Power off and reset or click STOP/RESET, then run again to see if the fault clears or recurs.
🛠 Step 2: Check Brake Circuit and Feedback Wiring
- After powering off, use a multimeter to measure the coil and feedback switch, confirming that the wiring is tight, the cables are undamaged, and there are no short circuits or open circuits.
⚙️ Step 3: Observe Brake Mechanical Status
- Manually operate the brake to detect any sticking, wear, or spring failure. If abnormalities are found, repair or replace as necessary.
🔧 Step 4: Adjust Inverter Parameters
- Enter Expert mode and adjust the following parameters sequentially:
- brH b2 = 1 (Enable feedback logic)
- bEt ≥ Actual brake release time
- Ibr, Ird to sufficient release current
- If bEn has an “automatic” mode, enable it; if controlling manually, disable it to avoid conflicts.
💡 Step 5: Monitor Operating Status
- After setting the parameters, observe the brake action response time to the inverter, feedback status, and status words to confirm that no further brF faults are reported.
🧩 Step 6: Fault Logging and Duty Strategy
- Summarize experiences, regularly inspect the brake and feedback components, establish maintenance norms, and perform regular resets and checks.
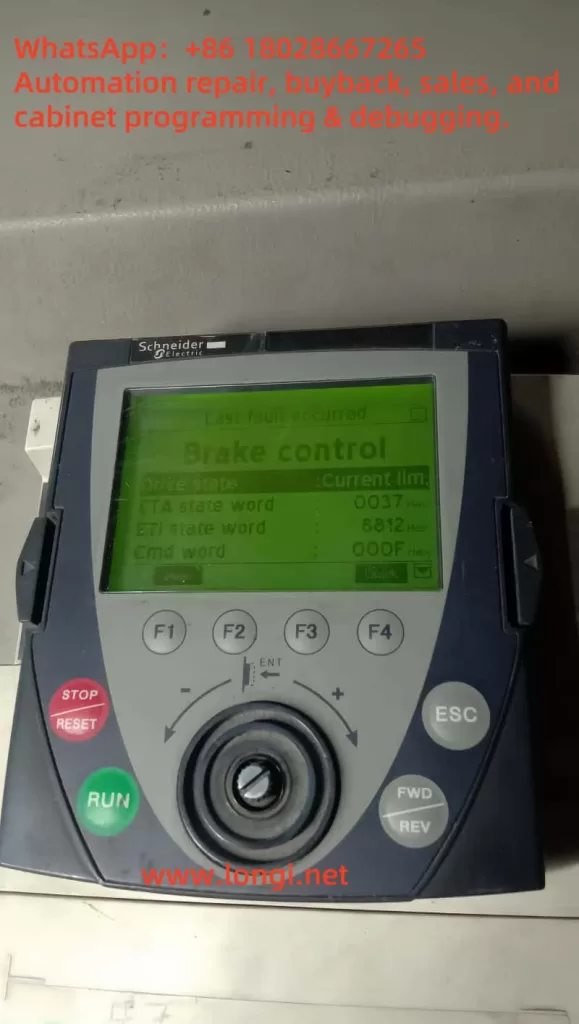
V. Developer and Engineering Recommendations
- If a third-party brake unit is used instead of a Schneider original, be sure to disable the internal cam cable control logic of the brake and fully outsource the control and feedback loops to the third-party system to avoid brF faults.
- Reasonably set automatic restart parameters (e.g., blF, obF may be set to Atr-) to allow automatic reset after the fault disappears, but a conservative mode is recommended to avoid restarting before the brake is released, which could cause injury or mechanical impact.
- Key on-site recommendation: Configure an alarm linkage strategy to monitor the BCA (brake contact alarm) and BSA (brake speed alarm) in the status words and promptly反馈 (feedback) abnormal states.
VI. Conclusion and Recommendations
Aspect | Recommendation |
---|---|
Parameter Settings | In Expert mode, correctly set key parameters such as brH b2, bEt, Ibr, Ird. |
Hardware Inspection | Inspect the brake mechanical status, coil, feedback switch, and wiring together. |
Process Strategy | Clarify the maintenance boundaries between electrical control and mechanical feedback logic to avoid internal and external conflicts. |
Maintenance System | Establish a regular inspection system, save fault records, and ensure long-term safe operation. |
🔚 Conclusion
Brake control faults (brF / bLF) in the ATV71 series are often caused by a lack of synchronization between logic and actual actions. By adopting a three-pronged approach of hardware detection, feedback verification, and parameter tuning, the root cause of the fault can be effectively located. After enabling Expert parameters, the inverter will intelligently distinguish between brake action time and feedback contact response, avoiding false alarms and improving system stability. It is hoped that the systematic analysis and references provided in this article will offer practical assistance in resolving brake system issues and ensuring reliable equipment operation.
If you still have questions or require further diagnosis, you can consult the official user manual or contact Schneider’s after-sales technical support for rapid assistance.