Introduction
The Hilectro HI200 series servo drives are widely utilized in industrial automation for their high-performance capabilities, enabling precise control of servo motors to achieve efficient and accurate production processes. However, in practical applications, various faults may arise, with ER062 (phase current acquisition fault) being a common error code. This fault typically indicates an issue with the drive’s ability to acquire or measure phase current. If left unaddressed, it can lead to drive or motor damage and disrupt the stability of an entire production line.
This article leverages the user-provided screenshots and servo drive manual, combined with general servo drive troubleshooting expertise, to provide a detailed explanation of the potential causes, diagnostic steps, and solutions for the ER062 fault. The goal is to offer clear, logically sound, and practical guidance to help users resolve this issue effectively.
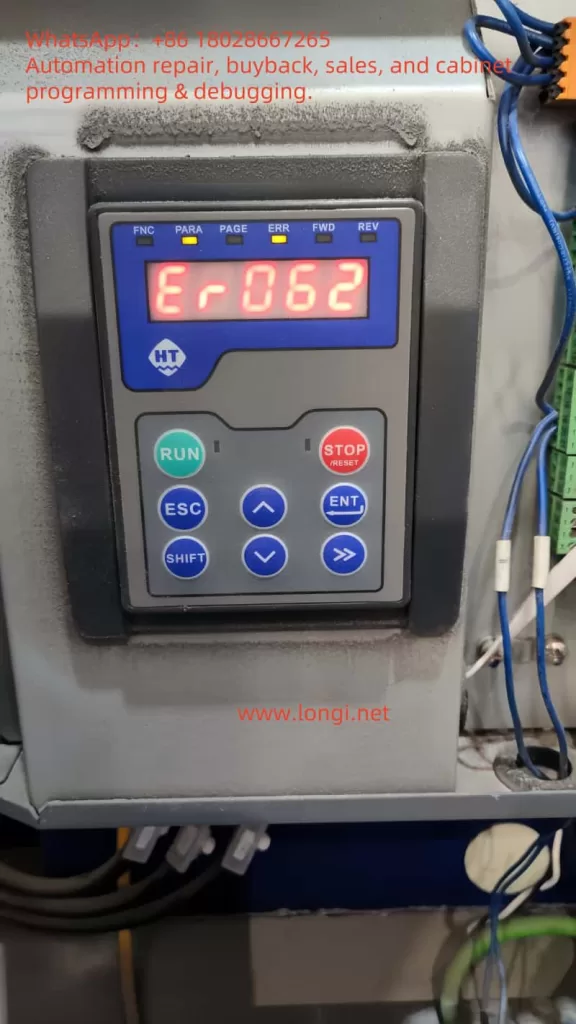
Section 1: Understanding the ER062 Fault (Phase Current Acquisition Fault)
1.1 What is Phase Current?
Phase current refers to the current flowing through each phase (A, B, C) in a three-phase AC system. In servo drives, measuring and controlling phase current is critical, as it directly impacts motor performance and protection mechanisms. Drives use current sensors (such as Hall effect sensors or shunt resistors) to acquire phase current, which is then processed by the control circuitry for vector control, overcurrent protection, and other functions.
1.2 Meaning of the ER062 Fault
The ER062 error code signifies a fault in the drive’s phase current acquisition process. Specifically, this could mean:
- The drive fails to accurately read or process phase current signals.
- There is an issue with the phase current acquisition circuit, such as a faulty sensor, broken wiring, or short circuit.
- An abnormality exists within the drive’s internal control circuitry.
As ER062 is specific to the Hilectro HI200 series, referencing the provided manual (Attachment ID: 2) or user screenshots (Attachment ID: 0) is essential for precise details. The flowchart (Attachment ID: 0) groups ER062 with ER057 and ER061 under phase current acquisition faults, suggesting a potential hardware or connection issue.
1.3 Why Phase Current Acquisition Faults Matter
Phase current acquisition is a core function of the drive. A fault in this area can result in:
- Inaccurate motor control, affecting position or speed precision.
- Disabled overcurrent protection, increasing the risk of motor or drive damage.
- Reduced overall system stability, impacting production efficiency.
Prompt diagnosis and resolution of the ER062 fault are therefore crucial.
Section 2: Common Causes of the ER062 Fault
Based on the characteristics of the Hilectro HI200 series and typical servo drive failure modes, the ER062 (phase current acquisition fault) may stem from the following causes:
2.1 Connection Issues
- Loose or Disconnected Cables: If the connection cables between the drive and motor (especially current acquisition lines) are loose or broken, the drive may fail to acquire phase current.
- Improperly Seated Plugs: The current acquisition module may rely on plugs, and poor contact due to incomplete insertion can trigger the fault.
2.2 Sensor Failures
- Damaged Current Sensors: Faulty sensors (e.g., Hall effect sensors or shunt resistors) due to aging or overloading can disrupt current acquisition.
- Calibration Issues: Uncalibrated sensors may prevent the drive from accurately reading phase current values.
2.3 Wiring Problems
- Short Circuits or Open Circuits: A short or open in the phase current acquisition wiring (from motor to drive) can compromise signal integrity.
- Interference or Noise: External electromagnetic interference or noise in the wiring may cause the drive to misinterpret current signals.
2.4 Internal Drive Issues
- Control Board Failure: The control board, responsible for processing current signals, may malfunction due to chip damage or poor soldering.
- Firmware or Software Bugs: Though rare, an outdated firmware version or software glitch could affect current acquisition functionality.
2.5 Motor Issues
- Short or Open Windings: Internal motor winding faults can disrupt normal phase current flow, leading to acquisition errors.
- Faulty Motor Cables: Damaged or poorly connected motor cables may also contribute to the problem.
2.6 Environmental Factors
- High Temperature or Dust: Excessive heat or dust accumulation can destabilize internal components like sensors or connectors.
- Vibration or Shock: Industrial vibrations or impacts may loosen connections or damage components.
The following table summarizes potential causes of the ER062 fault and their characteristics:
Cause Category | Specific Cause | Symptoms/Characteristics |
---|---|---|
Connection Issues | Loose or disconnected cables, unseated plugs | ER062 appears; may resolve temporarily after reseating |
Sensor Failures | Damaged sensors, calibration errors | Abnormal or missing phase current signals |
Wiring Problems | Short circuits, open circuits, electromagnetic interference | Unstable current signals, possible additional electrical faults |
Internal Drive Issues | Control board failure, firmware bugs | Persistent fault despite normal connections |
Motor Issues | Short or open windings, faulty cables | Motor runs abnormally, possibly with overheating |
Environmental Factors | High temperature, dust, vibration | Intermittent faults linked to environmental changes |
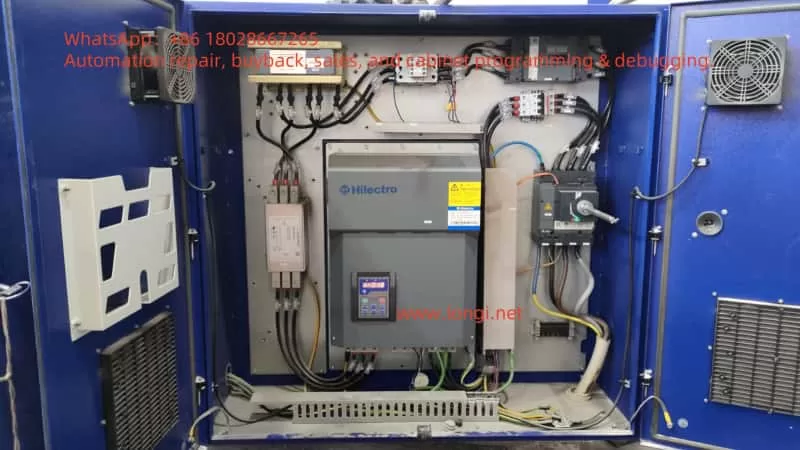
Section 3: Diagnostic and Resolution Steps for ER062 Fault
Below are detailed diagnostic and resolution steps for the ER062 fault in the Hilectro HI200 series, based on the user’s flowchart (Attachment ID: 0) and general servo drive troubleshooting practices.
3.1 Verify Phase Current Status
- Steps:
- Use a multimeter or oscilloscope to check the phase current signals on the A, B, and C phases.
- Ensure the current waveforms are sinusoidal and within expected values during normal operation.
- Judgment:
- If phase current is abnormal (e.g., no signal or erratic readings), the issue may lie in connections or wiring.
- If phase current is normal but ER062 persists, an internal drive problem is likely.
- Tools: Multimeter, oscilloscope.
3.2 Inspect Connections
- Steps:
- Ensure the cables between the drive and motor (especially current acquisition lines) are secure.
- Check that plugs are fully inserted and contacts are good.
- Reseat cables if necessary.
- Precautions:
- Disconnect power before inspecting to avoid electrical hazards or equipment damage.
- This is the first step recommended by the flowchart (Attachment ID: 0).
3.3 Troubleshoot Wiring and Sensors
- Steps:
- Use a multimeter to test the phase current acquisition wiring for short circuits or open circuits.
- If accessible, verify the output of the current sensors.
- Precautions:
- Replace damaged wiring if found.
- Replace the sensor module if defective (refer to the manual, Attachment ID: 2).
3.4 Check Internal Drive Components
- Steps:
- If prior steps fail, the issue may be an internal control board or firmware problem.
- Per the flowchart (Attachment ID: 0), if phase current is normal but the fault persists, return the drive to the factory for professional inspection.
- Special Note:
- For the Hi282 model, a boot alarm may require mainboard replacement.
- Reference: Hilectro HI200 Series Manual (Attachment ID: 2).
3.5 Inspect the Motor
- Steps:
- Use a multimeter to check motor windings for shorts or opens.
- Ensure motor cables are intact.
- Precautions:
- Replace or repair the motor if issues are detected.
3.6 Environmental Assessment
- Steps:
- Verify that the ambient temperature around the drive is below 40°C.
- Remove dust from the drive’s surface and ventilation areas.
- Precautions:
- Keep the drive away from strong electromagnetic interference sources.
3.7 Restart and Parameter Check
- Steps:
- Restart the drive to see if the fault clears.
- If possible, review drive parameter settings (e.g., current feedback gain) for accuracy.
- Precautions:
- Refer to the manual (Attachment ID: 2) for parameter details, ensuring settings match the application.
3.8 Contact Technical Support
- Steps:
- If all else fails, contact Hilectro technical support or arrange for factory service.
- Precautions:
- Provide the error code, model number, and a detailed fault description when seeking support.
The following table outlines the diagnostic steps and their priority:
Step | Priority | Tools Required | Expected Outcome |
---|---|---|---|
Verify Phase Current Status | High | Multimeter, oscilloscope | Confirm normal current signals |
Inspect Connections | High | None | Ensure secure connections |
Troubleshoot Wiring/Sensors | Medium | Multimeter | Rule out shorts or opens |
Check Internal Components | Medium | None (professional tools) | Determine need for factory service |
Inspect Motor | Medium | Multimeter | Exclude motor winding/cable issues |
Environmental Assessment | Low | None | Ensure suitable operating conditions |
Restart and Parameter Check | Low | None | Resolve temporary faults |
Contact Technical Support | Last Resort | None | Obtain professional assistance |
Section 4: Preventive Measures
To prevent the recurrence of the ER062 (phase current acquisition fault), users can adopt the following preventive strategies:
4.1 Regular Maintenance
- Periodically inspect drive-to-motor cable connections for tightness and plug integrity.
- Clean the drive’s surface and vents to prevent dust buildup.
4.2 Environmental Control
- Maintain operating temperatures below 40°C and humidity below 90%.
- Avoid installing the drive in areas prone to vibration or impact.
4.3 Parameter Management
- Regularly back up drive parameter settings for easy recovery during restarts or replacements.
- Understand parameter meanings before adjustments, referencing the manual (Attachment ID: 2).
4.4 System Monitoring
- Use monitoring systems to track drive performance, particularly phase current values.
- Set alarm thresholds to detect anomalies early.
4.5 Firmware Updates
- Check for and apply the latest firmware updates to address known issues.
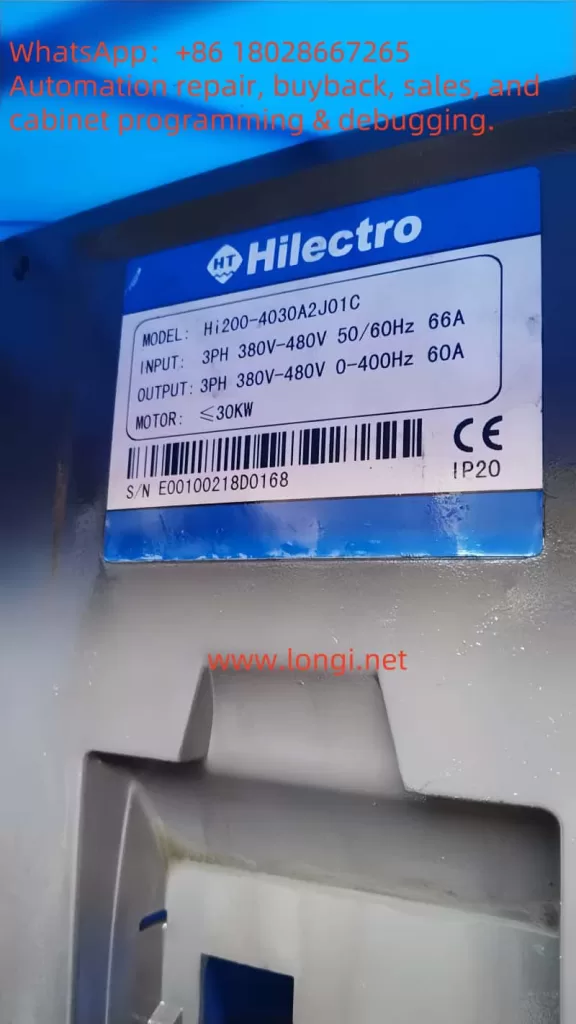
Conclusion
The ER062 (phase current acquisition fault) in Hilectro HI200 series servo drives, though common, can typically be resolved through systematic diagnosis and repair steps. This article, informed by user-provided screenshots and the manual, along with general servo drive troubleshooting knowledge, offers a comprehensive approach to addressing the issue.
It’s important to note that since ER062 is specific to the Hilectro HI200 series, users should prioritize consulting the official manual or contacting technical support for the most accurate guidance. If the problem cannot be resolved independently, returning the drive to the factory for professional servicing is recommended.
By implementing regular maintenance, environmental controls, and proper operating practices, users can significantly reduce the likelihood of ER062 faults, ensuring the stability and efficiency of their production systems.