1. Introduction
The Mitsubishi E700 series inverters, including the E740 model, are widely used high-performance devices in industrial automation, renowned for their efficiency, stability, and flexibility. However, during operation, these inverters may encounter faults, with the “E.AIE” fault code (Analog Input Error) being a common issue. This article provides an in-depth analysis of the E.AIE fault’s meaning, potential causes, and systematic troubleshooting steps and solutions to help users quickly identify and resolve the issue. Additionally, preventive measures are discussed to minimize the occurrence of similar faults.
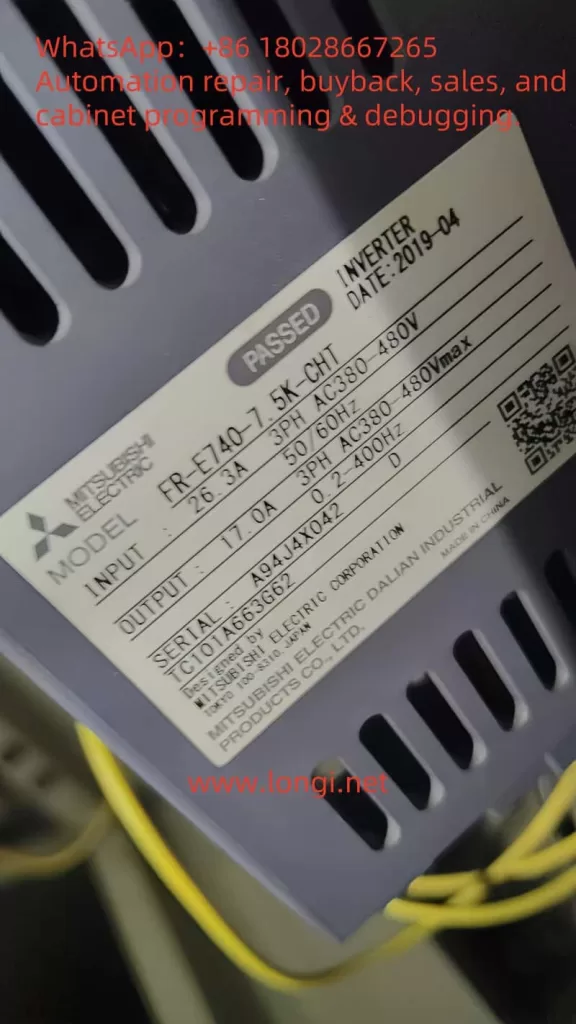
2. Meaning of the E.AIE Fault Code
According to the Mitsubishi E700 Inverter Manual (hereinafter referred to as the manual), the E.AIE fault code indicates an abnormality in the analog input. This fault is typically related to the analog input signals (e.g., 0-10V voltage or 4-20mA current) received through terminals (such as terminals 2 or 4), which are used to set motor operating frequency or other control parameters. When the inverter detects that these signals are out of range, missing, or unstable, it triggers the E.AIE protection function, halting output and displaying the fault code on the operation panel.
Possible Triggering Conditions
- Signal Out of Range: Input signal exceeds the inverter’s supported range (e.g., voltage > 10V or current > 20mA).
- Signal Transmission Issues: Wiring problems or electromagnetic interference causing signal interruption or distortion.
- External Device Failure: Malfunction of devices providing the signal (e.g., potentiometers, sensors, or PLCs).
- Parameter Setting Errors: Incorrect settings for parameters related to analog input, such as PR.73 and PR.267.
- Internal Inverter Issues: Damage to the analog input circuit.
Understanding the meaning of E.AIE allows for a multi-angle analysis of its causes and the development of troubleshooting strategies.
3. Possible Causes of the E.AIE Fault
The E.AIE fault may stem from external factors or issues within the device itself. The following is a detailed breakdown of potential causes:
3.1 Abnormal Analog Input Signal
The analog input signal is typically provided by an external device to control frequency or parameters. The manual (PAGE 71) notes that the E700 series supports 0-5V, 0-10V voltage inputs, and 4-20mA current inputs. If the signal exceeds these ranges, the inverter triggers protection.
- Possible Issues:
- Abnormal output from an external device (e.g., voltage exceeding 10V).
- Unstable or missing signal.
- Example: A damaged potentiometer causing voltage fluctuations, or a PLC output module failing, resulting in current exceeding 20mA.
3.2 Wiring Issues
Wiring problems are a common cause of analog input abnormalities. The manual (PAGE 19 and PAGE 23) provides detailed wiring requirements for control circuit terminals.
- Possible Issues:
- Loose or Disconnected Wiring: Poor contact at terminals 2 (voltage input), 4 (current/voltage input), or 5 (common terminal).
- Wiring Errors: Voltage signal mistakenly connected to a current terminal, or the common terminal not properly connected.
- Electromagnetic Interference: Unshielded signal lines or proximity to power lines causing signal distortion.
- Example: Signal lines not using shielded cables, affected by electromagnetic interference from nearby motor operation.
3.3 External Device or Sensor Failure
Analog signals are often sourced from external devices such as potentiometers, sensors, or PLCs. If these devices fail, it can lead to signal abnormalities.
- Possible Issues:
- Aged potentiometer causing unstable voltage output.
- Damaged sensor interrupting the 4-20mA current signal.
- Abnormal power supply to external devices affecting signal output.
- Example: A 4-20mA pressure sensor outputting abnormal current due to an internal short circuit.
3.4 Parameter Setting Errors
Inverter parameter settings directly affect analog input recognition. The manual (PAGE 49 and PAGE 71) highlights key parameters:
- PR.73 (Analog Input Selection): Defines the input type for terminal 2 (e.g., 0-10V or 4-20mA).
- PR.267 (Terminal 4 Input Selection): Defines the input type for terminal 4, supporting 0-5V, 0-10V, or 4-20mA.
- PR.125/PR.126 (Frequency Setting Gain): Calibrates the relationship between analog signals and frequency.
- Possible Issues: Mismatched settings for PR.73 or PR.267 with the actual signal type, preventing correct signal recognition.
- Example: PR.267 set to “0” (4-20mA) while the actual input is a 0-10V signal, leading to a read error.
3.5 Internal Inverter Circuit Failure
If external signals and wiring are normal but the fault persists, it may indicate a hardware issue.
- Possible Issues:
- Damage to the analog input circuit (e.g., A/D conversion module).
- Aging or moisture-related degradation of internal circuits.
- Example: Long-term operation in a humid environment causing circuit board corrosion.
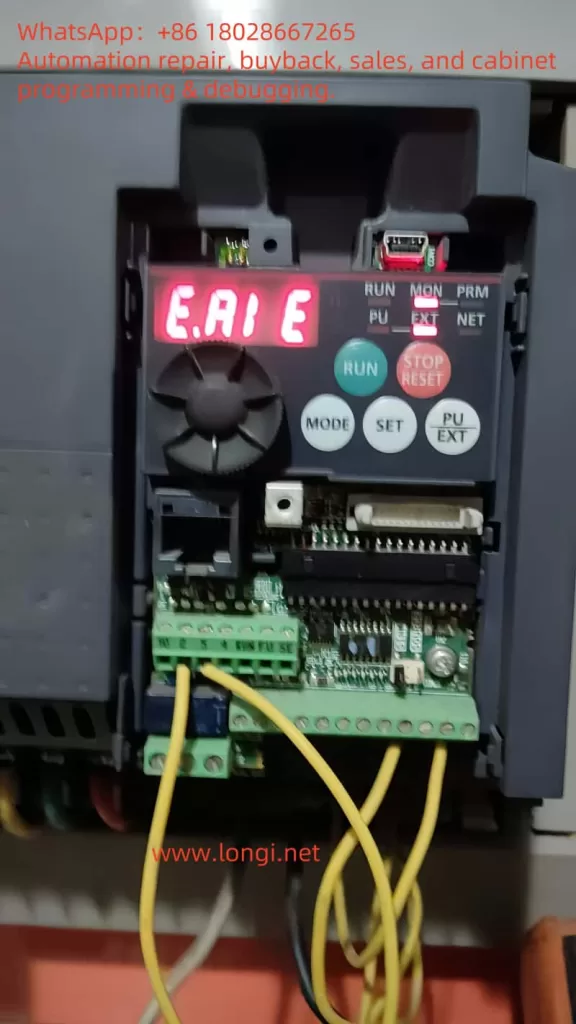
4. Role of PR.267 in the E.AIE Fault
PR.267 is a critical parameter related to analog input, specifically used to set the input type for terminal 4. According to the manual (PAGE 71), PR.267 options include:
- 0: 4-20mA current input.
- 1: 0-5V voltage input.
- 2: 0-10V voltage input.
The purpose of PR.267 is to inform the inverter how to interpret the analog signal received via terminal 4. For instance, if PR.267 is set to “0,” the inverter expects a 4-20mA current signal; if set to “2,” it expects a 0-10V voltage signal.
Relationship Between PR.267 and E.AIE Fault
When the PR.267 setting does not match the actual input signal type, the inverter may fail to recognize or process the signal correctly, triggering an E.AIE fault.
- Mismatch Example: If PR.267 is set to “0” (current input) but the input is a voltage signal, the inverter misinterprets the data, leading to an E.AIE error.
- Signal Out of Expected Range: Even with the correct signal type, if the PR.267 setting causes the inverter to expect a range that differs from the actual input (e.g., voltage input but exceeding 10V), a fault may occur.
Thus, checking the PR.267 setting is essential during E.AIE fault troubleshooting.
5. Steps to Resolve the E.AIE Fault
Based on the above causes, the following are systematic troubleshooting and resolution steps:
5.1 Check the Analog Input Signal
- Action:
- Use a multimeter to measure the signal between terminals 2 (voltage input) or 4 (current/voltage input) and terminal 5.
- Verify the signal is within the normal range (0-5V, 0-10V, or 4-20mA).
- Solution:
- If the signal exceeds the range, adjust the external device output.
- If the signal is missing, check the external device’s operation.
5.2 Inspect Wiring and Shielding
- Action:
- Check the integrity of terminals 2, 4, and 5 wiring, referring to the manual (PAGE 15) for the wiring diagram.
- Ensure signal lines use shielded cables with the shield grounded (PAGE 33).
- Solution:
- Tighten loose terminals or replace damaged wiring.
- Install shielded cables and keep them away from power lines to reduce interference.
5.3 Test External Devices
- Action:
- Disconnect the external device and use a signal generator to input a standard signal, observing if the fault disappears.
- Solution:
- If the fault resolves with a direct input, inspect and replace the faulty external device.
5.4 Check Parameter Settings (Focus on PR.267)
- Action:
- Enter parameter mode to verify PR.73 (terminal 2) and PR.267 (terminal 4) match the input signal types.
- Specific steps:
- Check the current value of PR.267.
- Confirm the actual signal type at terminal 4 (voltage or current).
- Adjust PR.267 to the matching value (e.g., “2” for 0-10V).
- Verify PR.125 and PR.126 are correctly calibrated (PAGE 70).
- Solution:
- Adjust PR.73 and PR.267 to the correct values.
- If unsure, reset parameters to factory settings (PAGE 42) and reconfigure.
5.5 Inspect Inverter Hardware
- Action:
- Check terminals for signs of burning or damage.
- If possible, replace the control board for testing.
- Solution:
- If hardware failure is confirmed, contact Mitsubishi service or a professional technician (PAGE 113).
5.6 Reset and Test
- Action:
- Press the “STOP/RESET” key to reset the fault (PAGE 95).
- Restart the inverter and conduct a trial run.
- Solution:
- If the fault persists, repeat the steps or seek technical support.
6. Preventive Measures
To reduce the occurrence of E.AIE faults, consider the following measures:
- Regular Wiring Checks: Inspect terminal integrity and signal line condition monthly.
- Use Quality Equipment: Select external devices compatible with the inverter.
- Optimize Installation Environment: Follow manual guidelines (PAGE 14) to avoid harsh conditions.
- Parameter Backup and Verification: Back up parameters after initial setup and periodically check PR.267 and other key settings.
- Regular Maintenance: Clean the inverter annually and inspect internal circuits as recommended (PAGE 113).
7. Case Study
Consider a FR-E740-7.5K-CHT inverter displaying an E.AIE fault:
- Troubleshooting: Measurement shows a 0-10V voltage input at terminal 4, but PR.267 is set to “0” (4-20mA).
- Root Cause: PR.267 mismatch with the actual signal type.
- Solution: Adjust PR.267 to “2” (0-10V), reset the inverter, and the fault is cleared.
- Prevention: Record PR.267 settings and regularly inspect external devices.
8. Conclusion
The E.AIE fault in Mitsubishi E700 (E740) inverters is typically caused by abnormal analog input signals, wiring issues, external device failures, parameter setting errors (especially PR.267), or internal hardware damage. By inspecting signals, wiring, devices, parameters, and hardware, users can effectively resolve the issue. Notably, correctly setting PR.267 is crucial to avoiding E.AIE faults. Preventive measures, such as regular parameter checks and backups, enhance equipment reliability. If troubleshooting proves challenging, contacting Mitsubishi technical support is recommended to ensure production efficiency and equipment safety.