Introduction
In the field of modern industrial automation, Variable Frequency Drives (VFDs) are core devices for controlling the speed of AC motors and are widely used in industries such as fans, pumps, packaging machinery, and textile machinery. The Andap VCD-2000 series VFD is favored by users for its high efficiency, stability, and ease of use. However, during operation, the VFD may trigger various fault codes due to different reasons, with E-30 being a common one. This article will delve into the meaning of the E-30 fault code, explore its possible causes, and provide detailed troubleshooting and solutions to help users quickly restore the normal operation of the equipment.
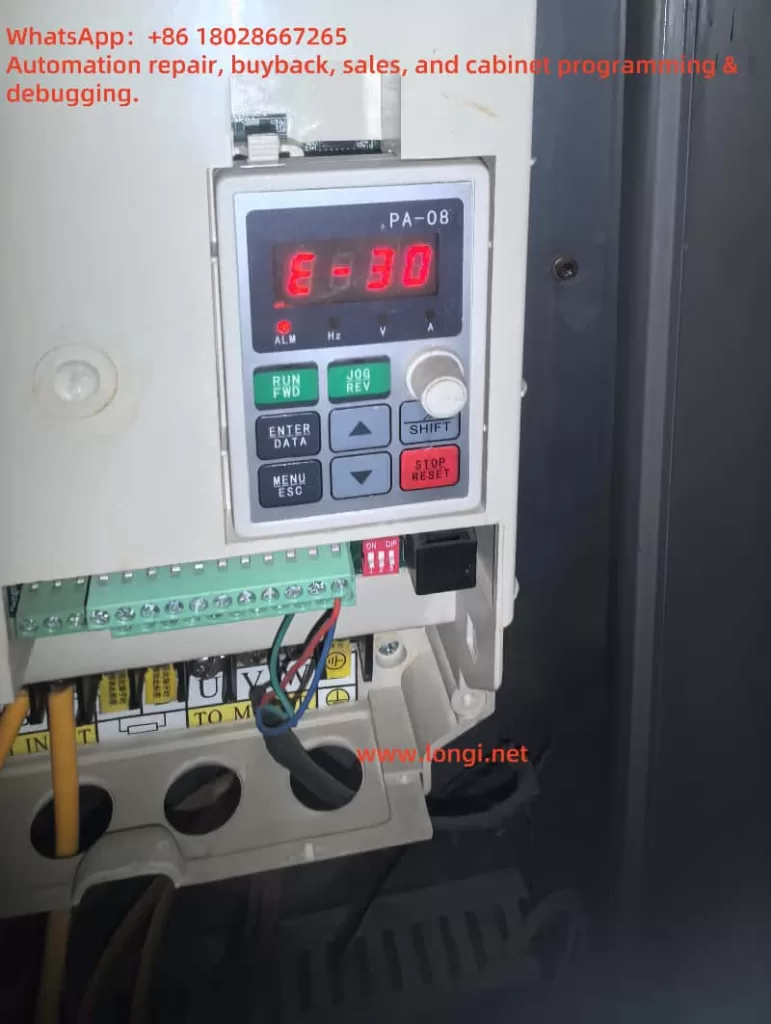
Overview of Andap VCD-2000 Series VFD
The Andap VCD-2000 series VFD is a high-performance vector control VFD launched by Andap. It employs highly intelligent IGBT modules and a 32-bit CPU dual-core processor, supporting current vector control technology to achieve precise torque and frequency regulation. This series of VFDs has the following characteristics:
- High Efficiency and Energy Saving: By optimizing the Space Vector Pulse Width Modulation (SVPWM) modulation technology, it achieves efficient energy conversion and significant energy-saving effects.
- Stable and Reliable: It supports sensorless vector control with a starting frequency range of 0.40Hz to 20.00Hz, adapting to various load requirements.
- Versatile: It offers multiple control methods such as constant torque V/F curves and automatic torque boost, suitable for applications like fans, pumps, and textile machinery.
- User-Friendly: Equipped with a simple operation panel, it supports various parameter settings and real-time monitoring, facilitating user operation and maintenance.
The VCD-2000 series is widely used in industrial scenarios such as constant pressure water supply, wire-cutting machines, and central air conditioning systems. However, even high-performance equipment may trigger fault codes due to external or internal factors, such as E-30.
The Role of VFD Fault Codes
VFD fault codes are an internal diagnostic system of the device, used to issue warnings to users when abnormal conditions are detected. These codes usually correspond to specific fault types, such as overcurrent, overvoltage, overheating, or module failure. By displaying fault codes, the VFD can:
- Quickly Locate Problems: Help users or technicians identify the cause of the fault promptly.
- Reduce Downtime: Shorten the troubleshooting and repair time through clear error prompts.
- Protect Equipment: Trigger protection mechanisms to prevent the fault from escalating and protect the VFD and connected equipment.
For the Andap VCD-2000 series VFD, the E-30 fault code is closely related to the protection mechanism of the power module, indicating that the device has detected an abnormality that may cause serious damage.
Meaning of the E-30 Fault Code
The E-30 fault code represents “Module Drive Protection”. According to the provided documentation, E-30 is triggered when the VFD detects a possible short circuit during the power module drive process. The power module is the core component of the VFD, responsible for converting DC power to AC power to drive the motor. If a short circuit occurs within the module or in the external circuit, it may cause the module to overheat or be damaged. Therefore, the VFD will immediately stop operating and display the E-30 code.
Possible causes of “Module Drive Protection” triggering include:
- Internal Short Circuit in the Power Module: Damage to IGBTs or other components within the module, leading to a short circuit.
- External Circuit Short Circuit: Short circuits in the motor coil, connecting cables, or connectors.
- Abnormal Drive Circuit: Signal abnormalities in the module drive circuit, leading to a false short circuit detection.
Troubleshooting and Solutions for E-30 Fault
When the Andap VCD-2000 series VFD displays the E-30 fault, users can follow these steps for troubleshooting and resolution:
Step 1: Check for Output Short Circuit
- Operation: Disconnect the VFD from the load (motor) to ensure the VFD is in a no-load state.
- Test: Attempt to start the VFD and observe if the E-30 fault still appears.
- Judgment:
- If the fault disappears, the problem may lie with the motor or the connecting circuit.
- If the fault persists, the problem may be inside the VFD.
- Note: Check the motor coil, cables, and connectors for signs of burning, damage, or poor insulation.
Step 2: Check the External Circuit
- Operation: If the fault disappears in the no-load state, further check the external circuit.
- Method:
- Use a multimeter to measure the resistance of the motor coil to confirm if there is a short circuit.
- Check the connecting cables for damage, aging, or insulation layer peeling.
- Ensure the connectors are secure, with no looseness or corrosion.
- Judgment:
- If a short circuit is found, repair or replace the damaged components.
- If the external circuit is normal, proceed to the next step.
Step 3: Test and Replace the Motor
- Operation: Connect a known normal motor to the VFD.
- Test: Start the VFD and observe if the E-30 fault still occurs.
- Judgment:
- If the fault disappears, the original motor may have problems and requires further inspection or replacement.
- If the fault persists, the problem may be inside the VFD.
Step 4: Check the Internal Module of the VFD
- Operation: If the above steps cannot solve the problem, check the power module inside the VFD.
- Method:
- Contact professional technicians or the Andap official service center to use professional equipment to detect the power module.
- If the module is damaged, it may need to be replaced or the entire VFD may need to be replaced.
- Note: The power module involves high-voltage circuits. Non-professional personnel should not attempt to disassemble or repair it to avoid electric shock or further damage to the equipment.
Step 5: Refer to the User Manual
- Operation: Consult the user manual of the Andap VCD-2000 series VFD to find detailed descriptions of the E-30 fault.
- Suggestion: The manual usually contains a fault code table and model-specific troubleshooting steps, which may provide additional parameter adjustment suggestions.
Step 6: Contact Technical Support
- Operation: If the above steps cannot solve the problem, contact the company’s technical support or authorized service provider.
- Provide Information:
- VFD model (e.g., VCD2000-A2S0007B).
- Fault code (E-30).
- Operating conditions when the fault occurred (e.g., load type, ambient temperature).
- Troubleshooting steps already attempted.
- Reference: You can contact us for support.
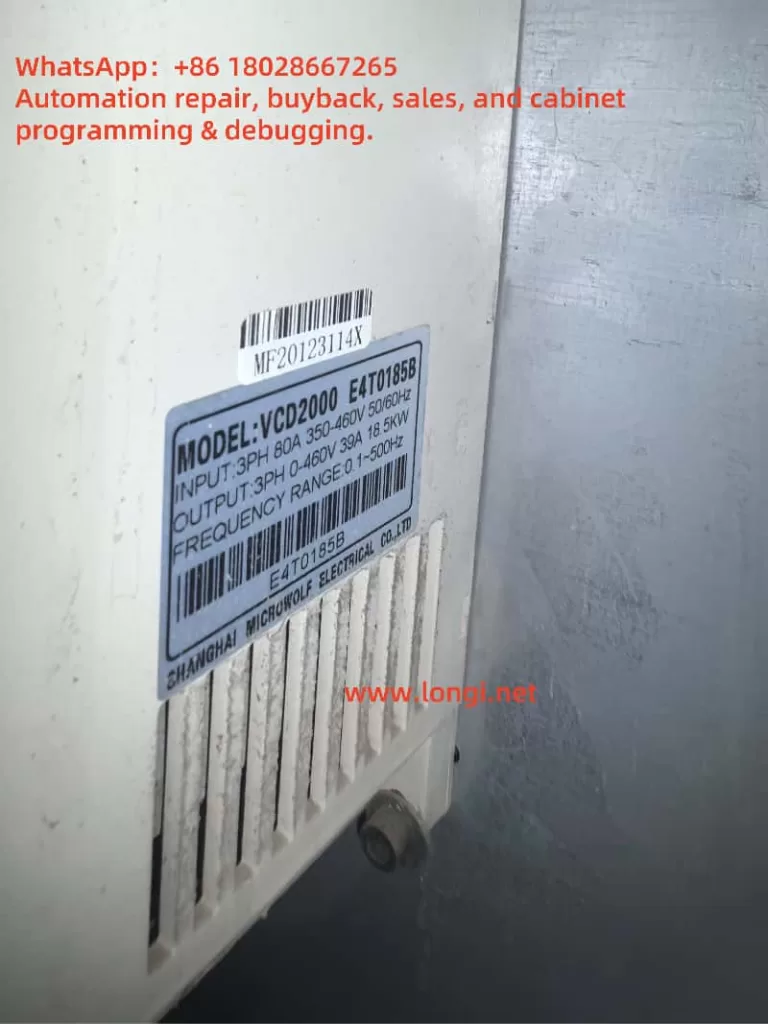
Preventive Measures for E-30 Fault
To reduce the occurrence of the E-30 fault, users can take the following preventive measures:
- Regular Connection Checks: Inspect the motor and VFD connecting cables monthly to ensure no looseness, damage, or corrosion.
- Maintain a Good Environment: Install the VFD in a dry, well-ventilated area, avoiding high temperatures (>40℃) or dusty environments.
- Load Management: Ensure the motor power matches the VFD’s rated power to avoid overloading.
- Regular Maintenance: Clean the heat sink, check the insulation performance, and update the firmware version according to the manufacturer’s recommendations.
- Firmware Updates: Check for new firmware versions and upgrade to optimize protection mechanisms and performance.
Conclusion
The E-30 fault code of the Andap VCD-2000 series VFD indicates that the power module drive protection has been triggered, usually caused by internal or external short circuits. Through systematic troubleshooting, including checking for output short circuits, testing the motor, and inspecting the internal module, users can effectively locate the problem and take appropriate measures. Regular maintenance and proper use are key to preventing such faults and ensuring the long-term stable operation of the VFD. If the problem is complex, it is recommended to contact professional technical support promptly to avoid further damage to the equipment.
Fault Troubleshooting Flow Chart
Step | Operation | Judgment | Next Action |
---|---|---|---|
1. Check Output | Disconnect the load and start the VFD | Fault disappears: External problem; Fault persists: Internal problem | Check the motor and cables |
2. Check External Circuit | Use a multimeter to check the motor and cables | Short circuit found: Repair; No short circuit: Continue | Replace and test the motor |
3. Replace Motor | Connect a normal motor and start | Fault disappears: Original motor problem; Fault persists: VFD problem | Check the power module |
4. Check Module | Contact professionals to detect the module | Module damaged: Replace; Module normal: Check the drive circuit | Contact technical support |
5. Refer to Manual | View the user manual | Specific instructions found: Follow the suggestions | Contact technical support |
6. Contact Support | Provide fault details | Obtain professional guidance | Repair according to the guidance |