1. Introduction: Symptoms and Background
In Schneider Electric’s Altivar ATV310 variable frequency drive (VFD), users may occasionally encounter the code --06
displayed on the integrated 7-segment LED screen. This condition is often accompanied by the motor being unable to start or respond to frequency commands. Although this may look like a fault, --06
is not an error code, but rather a status indication representing a special operating condition—usually “Freewheel Stop.”
This article explains the meaning of --06
, identifies common causes, and walks you through practical steps to resolve the issue and restore normal operation.
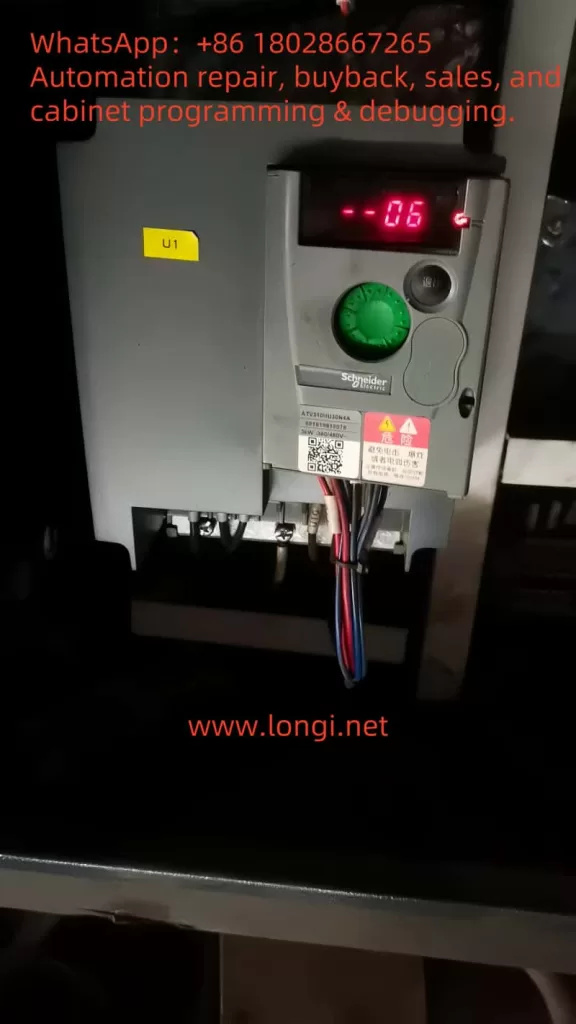
2. What Does --06
Mean?
The display code --06
on the ATV310 is an operational status code indicating that the drive is currently in Freewheel Stop mode, meaning output is disabled and the motor is freely coasting. This state is not caused by a fault but is often the result of control logic, input conditions, or communication states.
Other common drive statuses include:
--00
: Drive ready (no run command)--01
: Fast stop--06
: Freewheel stop
While the drive is in --06
, no output frequency is generated—even if run commands are issued—until the condition is cleared.
3. Common Causes of --06
Status
Several typical reasons could trigger the --06
state:
🟠 a. Logic Input Assigned to Freewheel Stop
If a digital input (e.g., LI1–LI4) is assigned to the Freewheel Stop function and is active, the drive will enter --06
.
🟠 b. Incorrect Run Command in 2-Wire or 3-Wire Mode
- In 2-wire mode (P201 = 2C), the drive needs a level-type run signal on LI1.
- In 3-wire mode (P201 = 3C), a pulse-style start and stop logic is used.
If wiring or configuration mismatches occur, the drive may fall into--06
.
🟠 c. Serial Communication Without Proper Commands
If you’re controlling the drive via Modbus or RS-485, and the master does not send a valid start command (bit 0x6 = 1), the drive enters --06
.
🟠 d. Analog Input Loss or Signal Drop
When using 4–20 mA input for speed control, a loss of input signal could trigger a fallback to freewheel stop.
🟠 e. Stop Button or Remote Stop Triggered
If the STOP key on the panel or an external STOP command is active, the drive may enter --06
.
🟠 f. Residual State After Power Cycle
Sometimes the drive reboots directly into --06
if the prior control signals remain unchanged.
4. Step-by-Step Troubleshooting and Recovery
✅ Step 1: Check Control Mode and Logic Inputs
- Confirm the control mode: P201 (2-wire/3-wire/serial).
- Check P202, P203 for proper assignment of RUN/STOP logic inputs.
- Use monitor mode (parameters 800–811) to observe input signal status.
✅ Step 2: Inspect Physical Inputs
- Check if any logic inputs (e.g., LI1) are incorrectly triggered.
- Look for short circuits, faulty switches, or wiring issues.
✅ Step 3: Check Analog/Serial Communication Settings
- For analog control, verify AI1 input signal and scaling.
- For Modbus, confirm that the master is sending the appropriate control word (bit 0x6 = 1).
✅ Step 4: Clear the Freewheel Stop and Restart
Option 1: Via Panel Navigation
- Press
ESC
orMODE
on the HMI. - Exit back to the main screen, wait for
rdY
(ready) to appear.
Option 2: Power Cycle
- Power off the drive for 10 seconds, then power it back on.
- The screen should return to
--00
orrdY
.
Option 3: Reassign Input Functions
- Use P202 to change logic input function from Freewheel Stop to an unused input.
- Set unused inputs to
No Function
(typically code 00).
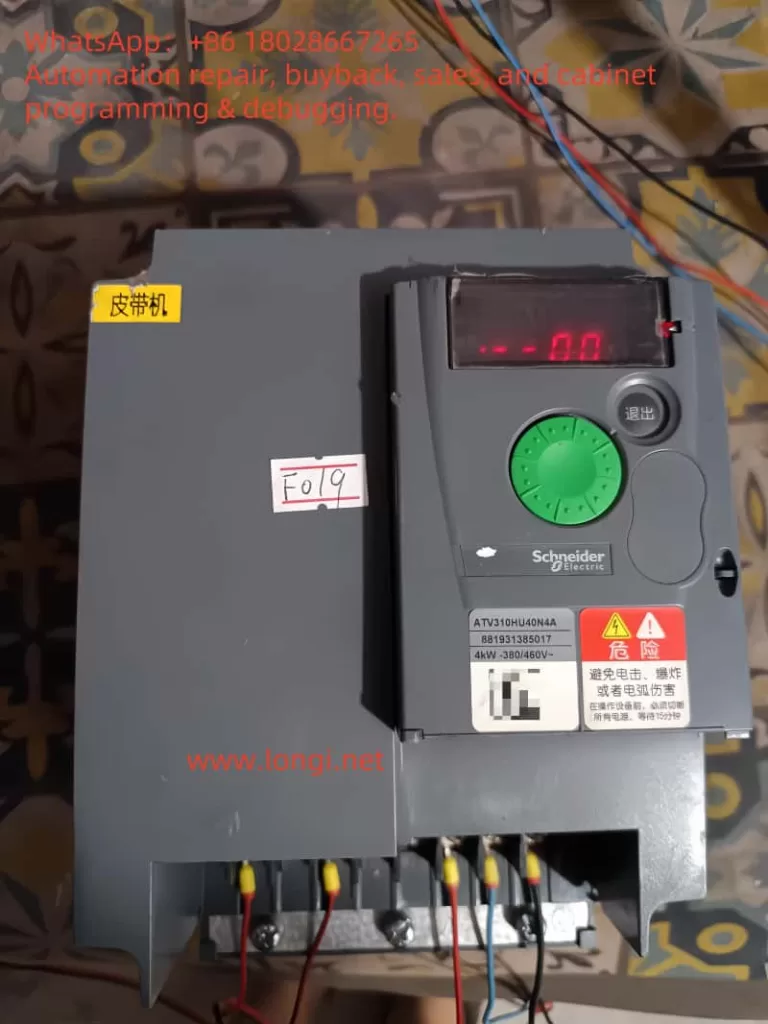
5. Ensuring Stable Operation After Recovery
After returning to normal status, take the following steps to avoid future issues:
- ✅ Reassign logic inputs only when needed.
- ✅ Avoid assigning STOP or Freewheel functions to frequently active lines.
- ✅ Add debounce and safety logic in PLC/HMI control.
- ✅ Enable fault auto-restart (parameter 602.0 = 01).
- ✅ Use clear feedback loops if controlling via communication protocol.
6. Summary Table
Step | Description |
---|---|
Identification | --06 is Freewheel Stop, not a fault |
Analysis | Check logic input functions, run mode, communication |
Resolution | Navigate panel, correct wiring or reset power |
Optimization | Adjust input definitions and enable self-recovery logic |
7. Conclusion
The --06
display on a Schneider ATV310 is a common condition that can interrupt motor operation but is not an error. With proper diagnosis—by inspecting control signals, input assignments, or communication—this state can be quickly cleared.
Once resolved, implementing preventive logic configuration and enabling smart restart strategies can ensure robust and continuous drive performance in both standalone and automated systems.
If issues persist, contacting Schneider’s technical support or reviewing the full parameter manual is recommended.