Abstract
This article provides a detailed analysis of the E.ou2 fault (overvoltage during constant speed operation) in the Mitsubishi FR-A700 series inverter. By integrating manual content with real-world application scenarios, it explores the causes, troubleshooting steps, and solutions to help users quickly diagnose and resolve the issue, ensuring stable equipment operation.
Keywords
Mitsubishi FR-A700, E.ou2 fault, overvoltage during constant speed, inverter, regenerative energy
1. Introduction
The Mitsubishi FR-A700 series inverters are widely recognized for their excellent performance in industrial motor control, particularly in applications like injection molding machines. However, during operation, inverters may trigger fault codes such as the user-reported “E.ou2.” According to the manual and the screenshot provided by the user, E.ou2 indicates an “overvoltage during constant speed operation,” meaning the main circuit DC voltage exceeds a safe threshold during fixed-speed operation, activating the protection mechanism. This article delves into this fault and offers practical solutions.
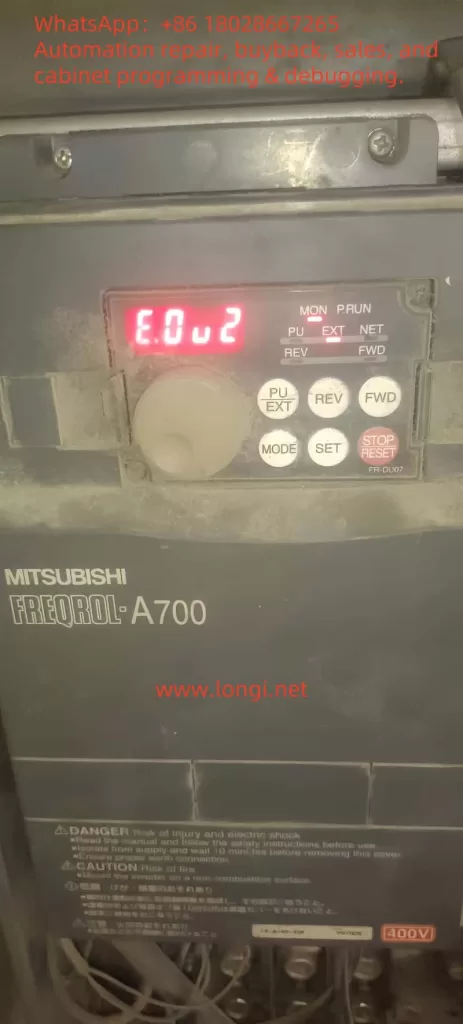
2. Definition and Causes of the E.ou2 Fault
The E.ou2 fault is a protective error code in the Mitsubishi FR-A700 inverter, specifically denoting “overvoltage during constant speed operation.” When the inverter detects that the main circuit DC voltage surpasses the specified limit (typically related to the power supply voltage and device configuration, e.g., a threshold in a 400V system), it automatically stops output to safeguard the equipment. The primary causes of this fault include:
- Excessive Regenerative Energy: During constant speed operation, the motor may generate significant regenerative energy due to load characteristics or mechanical inertia, feeding back into the inverter’s DC bus and raising the voltage.
- Improper Parameter Configuration: For instance, if Pr.22 (stall prevention operation level) is set too low, it may fail to effectively suppress voltage fluctuations.
- Abnormal Power or Load: Unstable power supply voltage or sudden load changes (e.g., process adjustments in an injection molding machine) may exacerbate regenerative energy production.
3. Fault Manifestations and Real-World Case
Based on the user-provided image, the inverter display clearly shows the “E.ou2” error code with the “RUN” light off, indicating that the device has stopped. This issue may occur in the following scenarios:
- Time Pattern: The user noted that the equipment runs normally in the morning but frequently faults at noon, possibly due to rising environmental temperatures or changes in production load.
- Industrial Environment: The image reveals dust accumulation on the inverter’s surface, suggesting prolonged operation in a harsh environment, which may impair heat dissipation and worsen the fault.
4. Troubleshooting and Solutions
To effectively address the E.ou2 fault, users are advised to follow these step-by-step troubleshooting and improvement measures:
4.1 Parameter Check and Adjustment
- Pr.22 (Stall Prevention Operation Level): Verify that this parameter is not lower than the motor’s no-load current. If it is, adjust it to a value higher than the no-load current to prevent erroneous protection triggers.
- Pr.882 ~ Pr.886 (Regenerative Feedback Function): Enable and optimize these parameters to manage regenerative energy effectively. Refer to page 365 of the manual for specific settings.
4.2 External Equipment Optimization
- Braking Unit: If regenerative energy is significant, installing a braking unit to dissipate excess energy through resistors is recommended.
- Common DC Bus Converter (FR-CV): For frequent overvoltage issues, using an FR-CV can efficiently absorb regenerative energy.
- Power Supply Inspection: Use a multimeter or oscilloscope to check the input power stability, ensuring voltage fluctuations stay within the inverter’s allowable range.
4.3 Environmental Improvements
- Heat Dissipation Management: Ensure proper ventilation for the inverter, adding fans or air conditioning, especially during high-temperature periods (e.g., noon).
- Cleaning Maintenance: Regularly remove dust from the inverter’s surface to prevent poor heat dissipation from causing cascading issues.
4.4 Data Logging and Analysis
- Operation Log: Record data such as load, speed, and environmental temperature at the time of the fault to identify potential patterns.
- Fault History: Use the inverter’s MON mode to review historical fault records for diagnostic support.
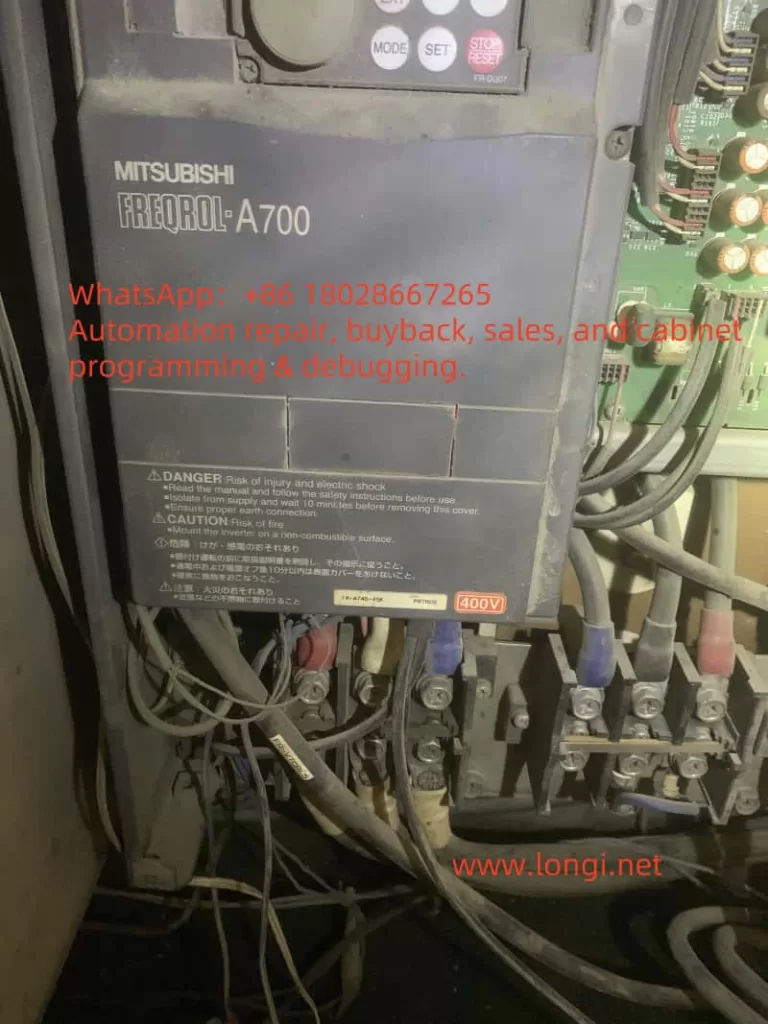
5. Case Analysis and Recommendations
Based on the user’s feedback and image data, the frequent occurrence of the E.ou2 fault at noon may be linked to the following factors:
- Temperature Impact: Rising environmental temperatures at noon reduce heat dissipation efficiency, making DC bus voltage more likely to exceed limits.
- Load Fluctuations: Production process adjustments may lighten the load, increasing regenerative energy.
For this scenario, the following recommendations are suggested:
- Enhance heat dissipation measures during high-temperature periods, such as temporarily adding fans.
- Investigate load characteristics during noon hours and adjust operating parameters or processes as needed.
- Implement regular maintenance to ensure long-term equipment stability.
6. Conclusion
The E.ou2 fault is a common overvoltage issue in Mitsubishi FR-A700 inverters during constant speed operation. By optimizing parameter settings, installing external equipment, improving heat dissipation, and conducting regular maintenance, users can significantly reduce fault occurrence and enhance equipment reliability. The troubleshooting steps and solutions provided in this article are universally applicable to similar scenarios.
7. References
- Mitsubishi FR-A700 Series Inverter User Manual