I. Product Overview & Core Features
The SJZO Frequency Inverter 200M Series is a high-performance vector control inverter designed for industrial automation, widely applied in motor speed regulation, energy-saving control, and precision drive scenarios. Its core advantages include a wide power range (0.4kW–500kW), high-precision control algorithms, and multifunctional interface design. This guide provides detailed instructions on operating panel functions, parameter setup techniques, external control implementation methods, and common fault troubleshooting.
II. Operating Panel Functions & Parameter Management
1. Operating Panel Overview
The SJZO 200M Series features an intuitive LCD operating panel supporting the following core functions:
- Start/Stop Control: Directly start or stop the motor via panel buttons.
- Frequency Setting: Adjust output frequency (0–400Hz) via a knob or digital input.
- Parameter Display & Modification: View real-time parameters such as current, voltage, and fault codes.
- Mode Switching: Toggle between local control (panel operation) and remote control (external signals).
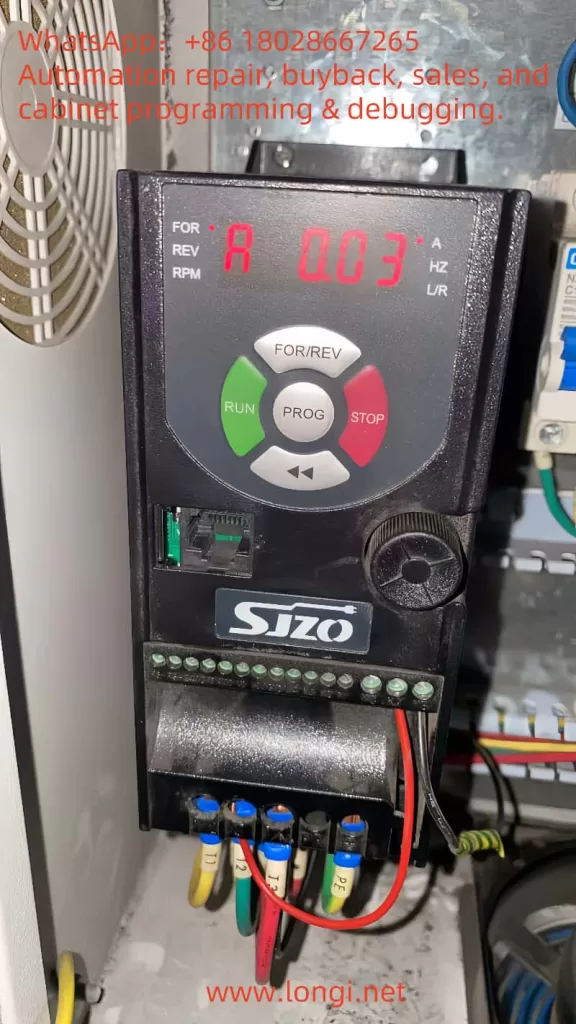
2. Password Setup & Removal
(1)Setting a Password
- Access parameter group
P7
(Access Control) and locate parameterP7.01
(User Password). - Enter a 4-digit password (e.g., 1234) and press “Confirm” to save.
- Once enabled, critical parameter modifications require password input.
(2)Removing the Password
- Access
P7.01
, enter the set password, and change the value to “0000” to remove it.
3. Parameter Access Restrictions
- Hierarchical Access Control:
- Parameter group
P7.02
allows setting different access levels (e.g., Engineer Level, Operator Level) to restrict unauthorized parameter modifications. - Example: Setting
P7.02
to “1” allows viewing only basic parameters; setting it to “2” grants full parameter modification access.
- Parameter group
4. Restoring Factory Default Settings
- Method 1: Panel Operation
- Press and hold the “Reset” button for 5 seconds until “INI” appears on the screen, then release. Parameters will automatically revert to defaults.
- Method 2: Parameter Setup
- Access parameter
P0.15
(Factory Reset), set it to “1,” and confirm. The inverter will restart with default settings.
- Access parameter
III. External Terminal Forward/Reverse Control & Potentiometer Speed Regulation
1. External Terminal Forward/Reverse Control
(1)Wiring Instructions
- Forward Terminal (e.g., X1): Connect to an external switch signal (normally open contact). Closing the contact starts the motor in the forward direction.
- Reverse Terminal (e.g., X2): Connect to another switch signal. Closing the contact starts the motor in reverse.
- Common Terminal (COM): Provides a reference ground for control signals.
(2)Parameter Setup
- Control Mode Selection:
- Set
P0.01=1
(External Terminal Control Mode).
- Set
- Terminal Function Definitions:
- Set
P4.01=1
(X1 as Forward Command),P4.02=2
(X2 as Reverse Command).
- Set
- Interlock Protection:
- Enable
P4.10=1
(Forward/Reverse Interlock) to prevent simultaneous activation and short circuits.
- Enable
2. External Potentiometer Frequency Regulation
(1)Wiring Instructions
- Potentiometer Connection:
- Connect the potentiometer ends to the inverter’s +10V (power supply) and GND (ground), and the wiper to the analog input terminal AI1 (or AI2).
- Signal Range: 0–10V corresponds to an output frequency range of 0–50Hz (adjustable).
(2)Parameter Setup
- Frequency Source Selection:
- Set
P0.02=2
(Analog Input AI1 as Frequency Setting Source).
- Set
- Input Range Calibration:
- Set
P3.01=0
(0–10V input),P3.02=50.00
(corresponding to a maximum frequency of 50Hz).
- Set
- Filtering Time:
- Adjust
P3.05=0.1s
(to reduce signal jitter interference).
- Adjust
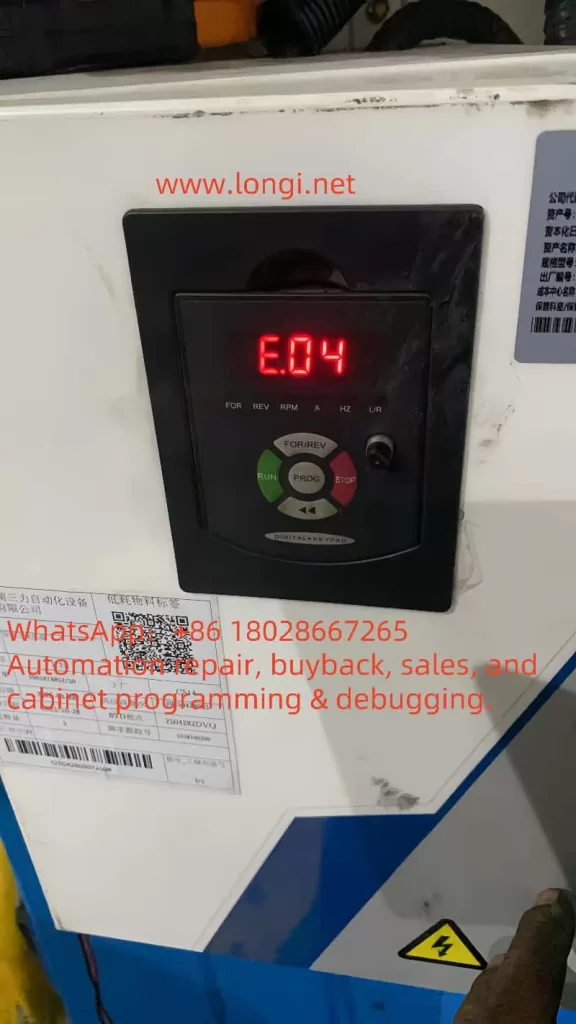
IV. E.04 Fault Code Analysis & Troubleshooting
1. Fault Definition
E.04 indicates “Output Overcurrent,” meaning the inverter detects motor current exceeding the rated threshold (typically 150%–200%). Common causes include:
- Motor winding short circuits or ground faults.
- Sudden load changes (mechanical jamming, abnormal drive system).
- Excessively short acceleration time (improper
P0.07
setting). - IGBT module damage or drive circuit failure.
2. On-Site Troubleshooting Steps
Step 1: Power-Off Inspection
- Disconnect power and measure the motor’s three-phase winding resistance to ensure balance (deviation ≤5%) and no grounding (resistance ≥5MΩ).
- Manually rotate the load to rule out mechanical jamming.
Step 2: Parameter Optimization
- Extend acceleration time: Adjust
P0.07
(Acceleration Time) to 10 seconds or more. - Reduce torque compensation: Modify
P3.12
(Torque Boost) to 5% or less.
Step 3: Hardware Inspection
- IGBT Module Testing:
- Use a multimeter’s diode mode to measure IGBT pins. Normal operation shows forward conduction and reverse cutoff. Replace the module if short-circuited.
- Current Sensor Check:
- Compare three-phase output current values. An abnormal phase may indicate a Hall sensor fault.
Step 4: Anti-Interference Measures
- Separate power and signal lines by ≥20cm.
- Install ferrite filters at both ends of analog signal lines.
3. Preventive Measures
- Regularly clean cooling air ducts to ensure proper fan operation.
- Avoid frequent starts/stops or overloading.
- Install input reactors (optional) in environments with significant grid voltage fluctuations.
V. Maintenance & Technical Support
- Routine Maintenance:
- Check terminal tightness monthly to prevent poor contact.
- Clean internal dust and replace aged capacitors quarterly.
- Professional Support:
- If the fault persists, contact us or consider equipment recycling services.
Conclusion
The SJZO Frequency Inverter 200M Series has become a cornerstone device in industrial automation due to its flexible control methods and high reliability. Mastering operating panel functions, external control implementation, and fault troubleshooting techniques can significantly enhance equipment efficiency and lifespan. For E.04 and other common faults, users can resolve issues through systematic troubleshooting. For complex cases, prompt professional support is recommended.