In the field of industrial automation, frequency inverters play a critical role in motor control. The stable operation of these devices is vital to maintaining production efficiency. The GTAKE GK820 series inverter, known for its performance and reliability, is widely used in various mechanical equipment. However, during operation, users may encounter OH-series fault codes (such as OH1, OH2, OH3), which indicate issues related to overheating protection. Understanding the causes and countermeasures for these faults is essential for maintenance and troubleshooting.
1. Overview of OH Fault Codes
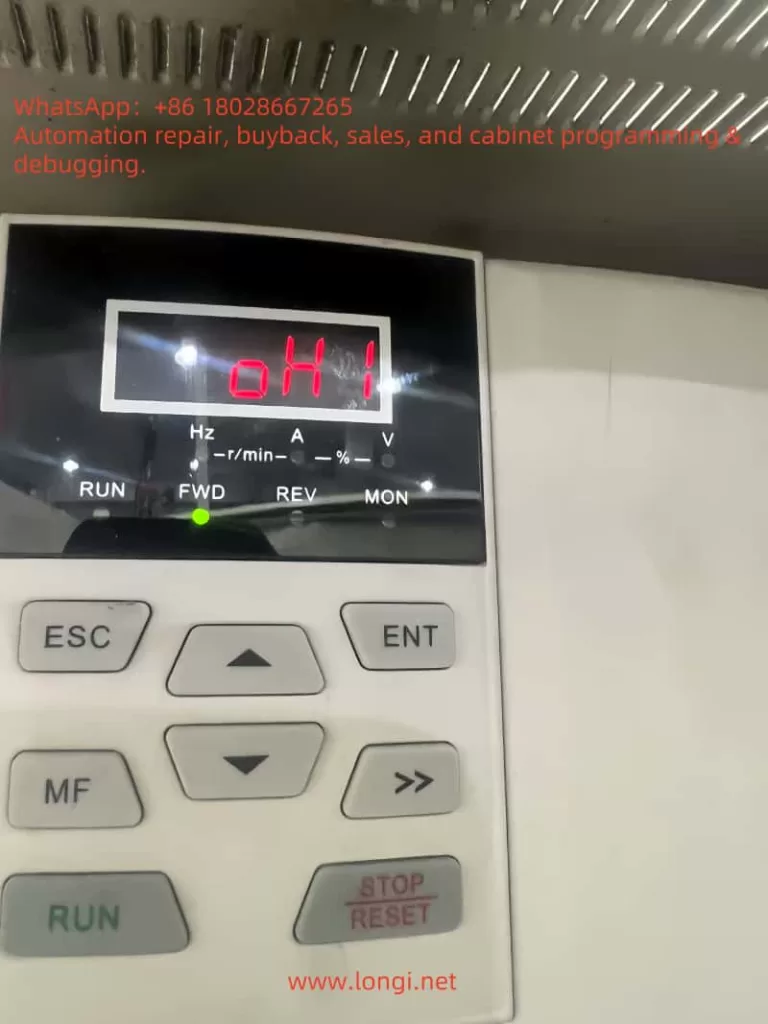
The OH-series fault codes on the GK820 inverter signify temperature-related issues that trigger automatic protection mechanisms. The main OH faults include:
- OH1: Heatsink Overtemperature
- OH2: External Thermal Protection Input
- OH3: Internal Module Overtemperature
When these faults occur, the inverter halts operation to prevent damage to internal components.
2. Root Causes of Each OH Fault
OH1: Heatsink Overtemperature
The heatsink is critical for dissipating the internal heat generated during inverter operation. When its temperature exceeds a safe threshold, the OH1 fault is triggered.
Possible Causes:
- High ambient temperature
- Dust accumulation or blocked airflow on the heatsink
- Fan failure or insufficient air volume
- Poor ventilation around the inverter
OH2: External Thermal Protection Input
OH2 faults are generally triggered by external thermal sensors (e.g., motor PTCs) connected to the inverter’s input terminal.
Possible Causes:
- High ambient temperature
- Incorrect thermal protection point setting
- Faulty or broken temperature detection circuit
- Poor contact or loose connection on the temperature sensor
OH3: Internal Module Overtemperature
OH3 indicates that the inverter’s internal components have exceeded their rated operating temperature.
Possible Causes:
- Internal fan malfunction
- Blocked internal air ducts
- Faulty internal circuit board
- Long-term overload operation without proper cooling
- Internal temperature detection circuit failure
3. Troubleshooting and Solutions
Resolving OH1 Fault:
- Check ambient temperature: Ensure the installation environment is below 40°C.
- Clean the heatsink: Remove dust and debris regularly to maintain airflow.
- Inspect the cooling fan: Verify that the fan is working properly; replace it if necessary.
- Improve ventilation: Leave enough space around the inverter for air circulation and avoid proximity to heat sources.
Resolving OH2 Fault:
- Check motor thermal sensor (PTC): Ensure correct type and proper installation.
- Verify parameter settings: Set the correct motor overheat protection threshold.
- Inspect signal wiring: Ensure the sensor wiring is securely connected and undamaged.
- Use shielded cable: Reduce electrical interference on sensor signals.
Resolving OH3 Fault:
- Inspect internal fans: Confirm proper operation and replace faulty fans.
- Clean internal components: Remove dust that may be affecting internal heat dissipation.
- Check module temperature detection circuit: Use a multimeter or diagnostic tool to verify if the circuit is working.
- Avoid overload operation: Reduce long-term full-load usage; apply load margins.
- Seek service: If the fault persists after inspection, contact GTAKE technical support.
4. Preventive Measures
- Routine cleaning: Clean air filters, fans, and heatsinks regularly to prevent dust accumulation.
- Ambient monitoring: Use sensors to monitor room temperature and humidity.
- Schedule maintenance: Periodically inspect terminal blocks, connectors, and sensors.
- Avoid overloading: Size the inverter and load correctly; prevent continuous operation at high torque.
- Install in suitable environments: Avoid corrosive gases, high humidity, or poor ventilation.
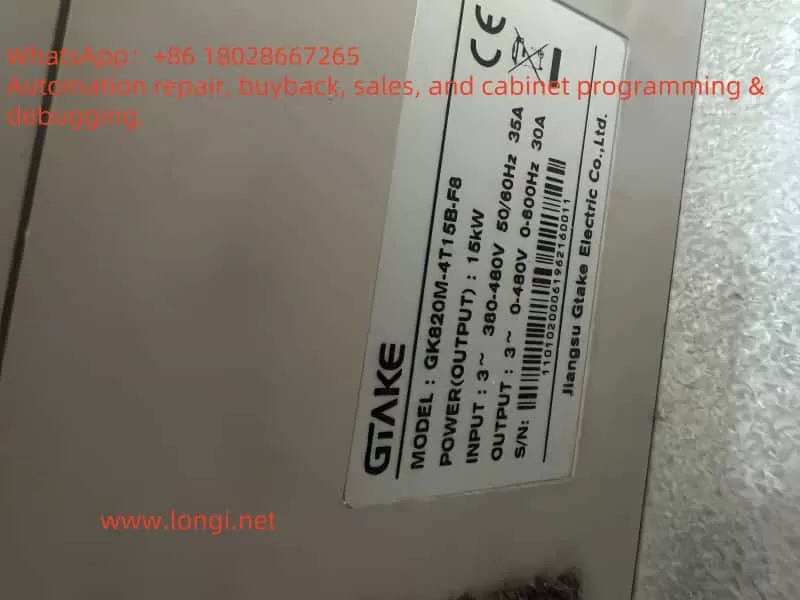
5. Summary
The OH fault codes in the GK820 series are designed to protect the inverter from damage caused by overheating. By identifying the specific fault (OH1, OH2, or OH3), users can systematically diagnose the root cause and take appropriate corrective actions. Preventive maintenance and environmental management are key to avoiding these issues.
Proper installation, regular inspection, and adherence to usage guidelines will significantly reduce the occurrence of thermal faults and extend the service life of the inverter. If problems cannot be resolved on-site, contacting professional technical support is recommended.